Kettlebell is a great weight for building strength and muscle. Appearing 350 years ago, kettlebells have evolved in many different styles and materials till now. But have you ever wondered: how to create kettlebells? and Do you know where do you should buy kettlebells?
As a company specializing in metal casting for many years, we will tell the story of kettlebells in this article. How are they being manufactured, and how customers have always been satisfied with our products.
Involving in the production process and fabricating thousands of kettlebells that serving the world need make us very proud of. And it is our pleasure to get satisfied feedback from our beloved customers for what we produced.
In the following, VIC will share the process of how to transform a pile of iron that seem useless to pretty kettlebells as favorite gym set of practitioners at Vietnam’s cast iron foundry.
Scroll down and dig out!
Kettlebell Design
Do you know why the kettlebell you are practicing every day is so comfortable to hold? To be able to create a kettlebell with a handle that fits well with a reasonable size, the kettlebell manufacturer had to learn, research and test through many different versions.
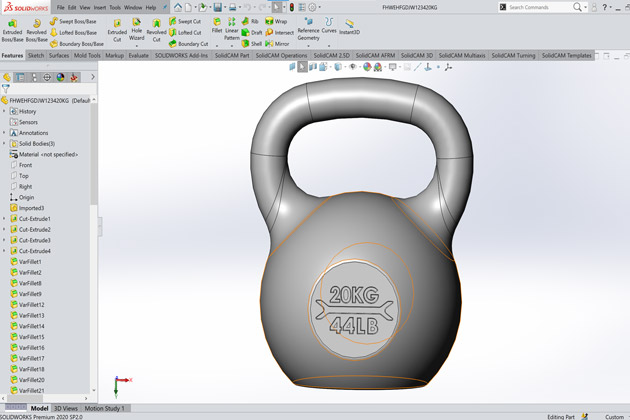
The material of kettlebell is usually cast iron or steel to ensure stiffness and durability.
The design of the kettlebell includes a bell with a handle. Just changing the design of the handle a bit, whether the diameter or the width will also affect the grip.
Whether you can perform the movements accurately and seamlessly or not depends a lot on the design stage.
Usually, kettlebell has two main types of handles: arc arms and straight arms.
The arc handle is easier to hold than the straight arm so it is suitable for beginners. The straight grip has less grip area, making it harder to hold with both hands so this type is suitable for experienced people.
Some of the trapezoidal or triangular handles are variations of kettlebells. These are harder to handle and our advice is not to try them.
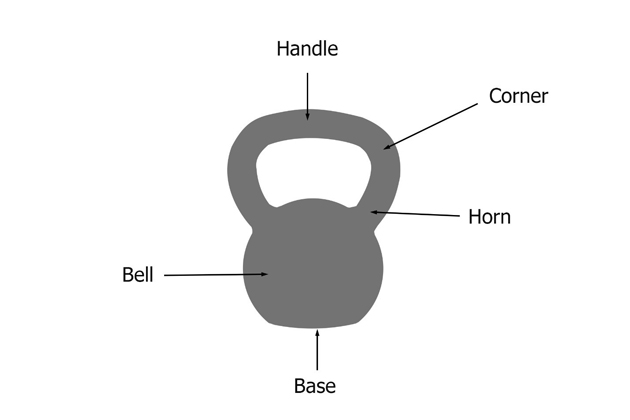
The horn part – the part that connects the handle and the bell also affects the way the weight is held. The size of the horn and the distance between the handle and the bell determines the grip space.
Horn and hollow core are the two main factors that change weight concentration. For weights without hollow core, weight concentration will not be put up near the handle so the feeling of exercise will not be good.
The corner can’t be too perpendicular either. Because it can cause injury to the little finger. The base must be flattened to maintain balance when placed on the floor.
The logo and number printing are also not too deeply cast to avoid affecting the balance.
The surface of the kettlebell is also an important consideration. The surface if too rough will cause hand pain, if it is too smooth, it will be easy to slippery. To provide a good grip, foundry often applies powder-coated moderately to conceal the protrusions.
You see, there are a hundred things to consider when designing kettlebells. We take all of that into account because we know a kettlebell is a daily companion, taking care of everyone’s health to their physique and weight.
Casting kettlebells
There are many different casting technologies, each with its own advantages and disadvantages affecting the quality and price of the product.
With kettlebells, we have the following casting technologies.
I. Lost foam casting
This is a molding technology that can ensure a balance between quality and price, the two main determinants of a customer’s purchase.
Learn about lost foam technology here.
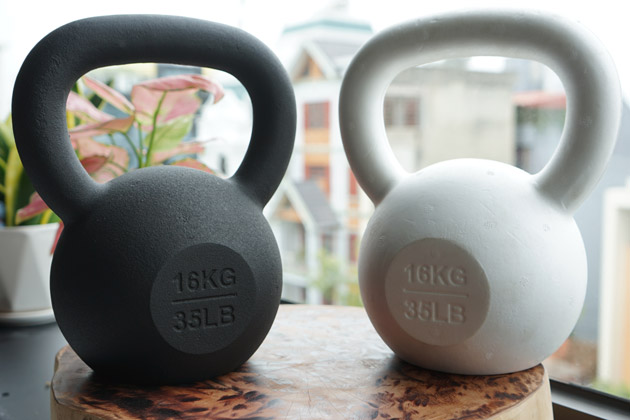
The steps to create kettlebell using lost foam technology are as follows:
Make kettlebell pattern
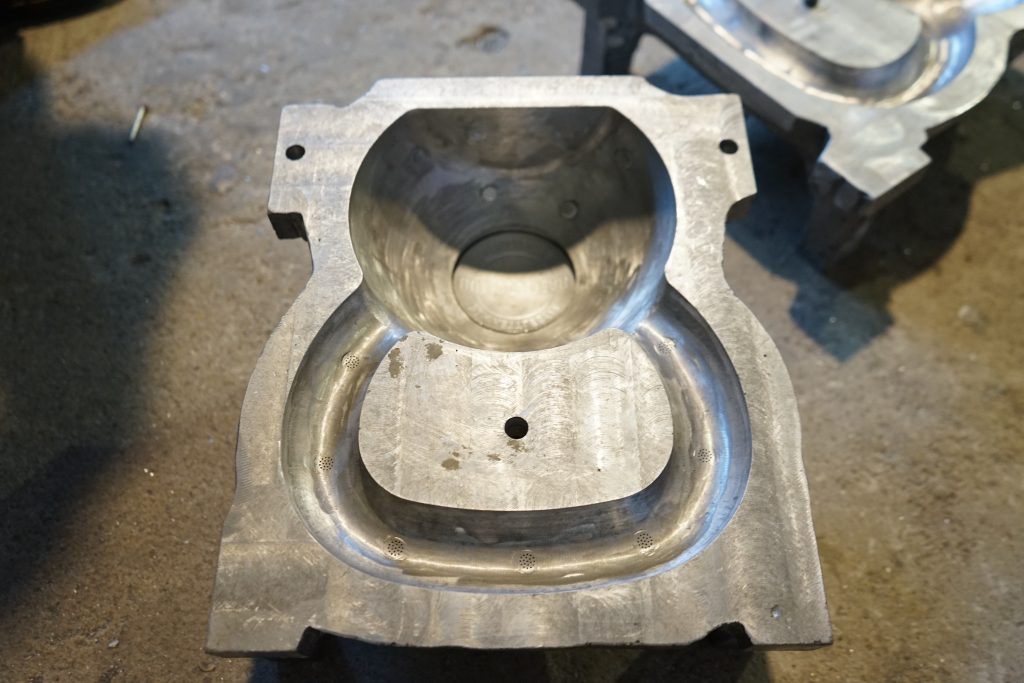
At VIC Foundry, the Kettlebell pattern is created by inserting foam particles (EPS) into the molding machine through a pre-foaming machine.
Then use the hot temperature to make the porous particles expand with a size 5 times larger to fill the mold.
The expanded foam will be pressed tightly and stick together and form a kettlebell shape, called the white foam pattern.
At this time, we will coat white foam patterns with heat-resistant paint and dry.
Pouring molten metal
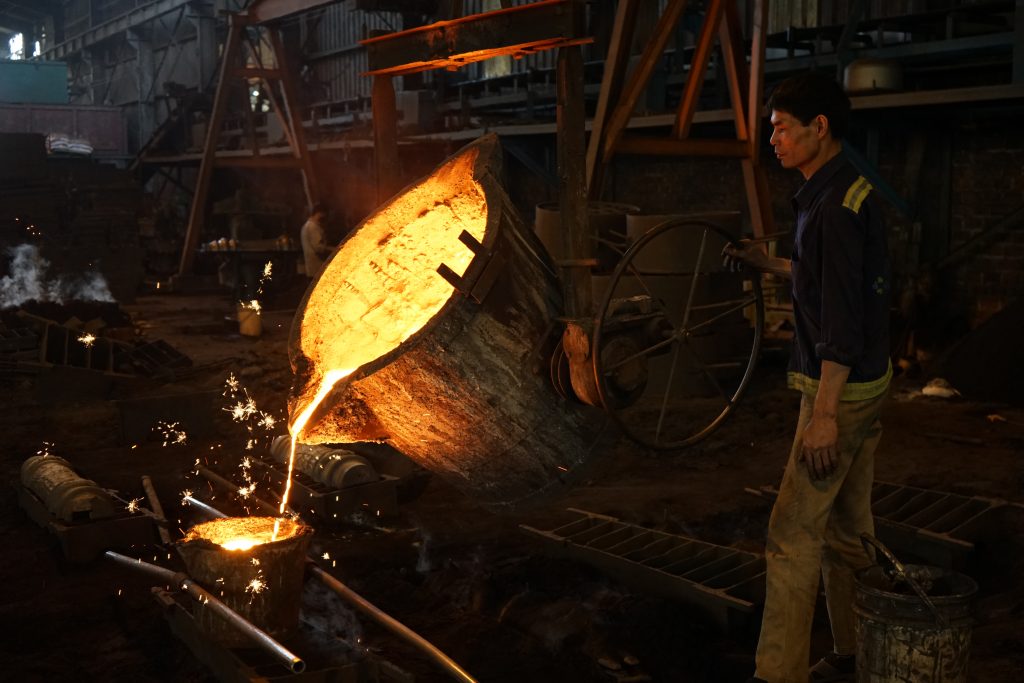
The metal materials that are mixed in the right proportions are fed into the furnace at a high temperature and converted to a liquid at a certain temperature. This stage is called melting metal.
At this point we have prepared a flask that matches the size of the pattern.
Kettlebell pattern after drying paint is placed into flask and filled with un-bonded sand and compacted. This is called a mould.
Start pouring the molten metal into the pattern container. The high temperature burns out the foam and the kettlebell shaped casting is formed in the mold. Each pattern can only be used once, so this casting technology will cost more to make the pattern than other technologies.
At this point just shaking the flask and take out the casting. The rough casting kettlebell is made.
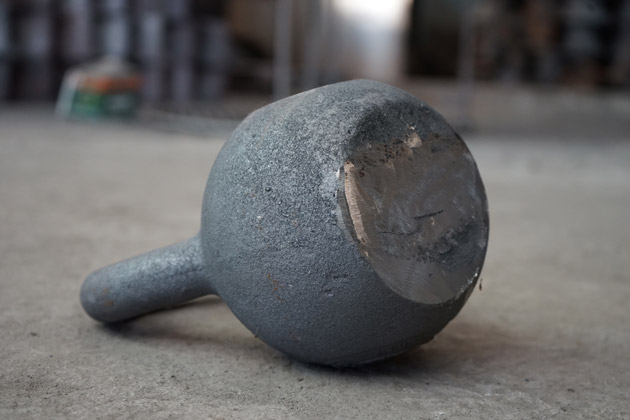
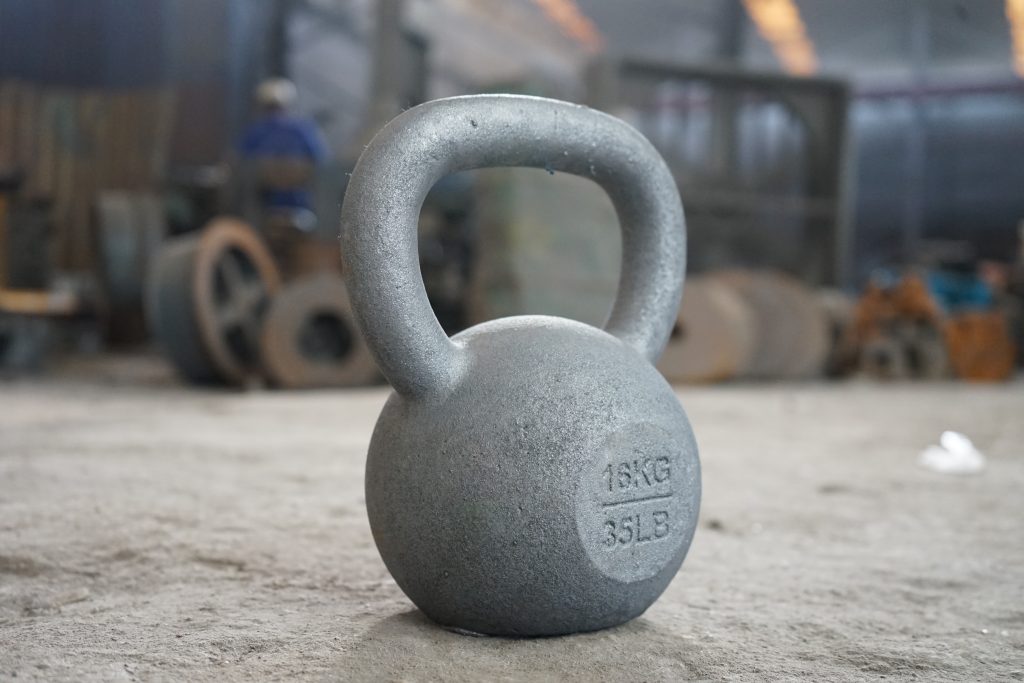
II. Greensand casting technology
Greensand technology is the most popular casting technology in the casting industry. Compared with Lost foam, green sand produces molding products with a slightly rougher surface but saves on pattern-making costs.
Learn green sand technology here.
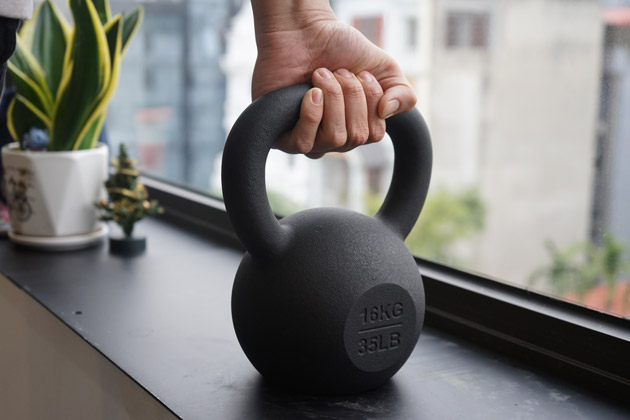
The process of casting kettlebell by green sand casting:
Make kettlebell pattern
Kettlebell pattern is made from aluminum, cut by CNC machine into two halves of pattern, called cope and drag.
With the green sand technology, a pattern is used for mass production of kettlebells.
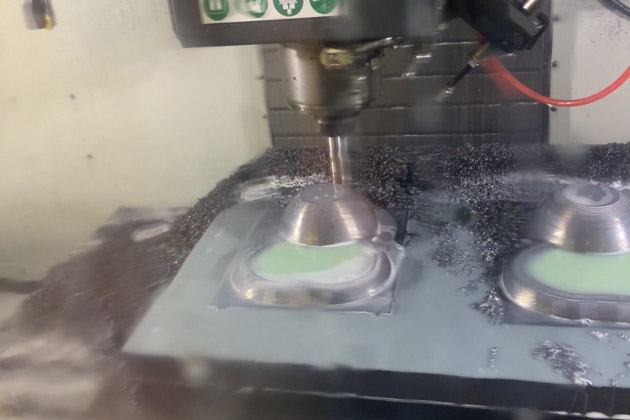
Read more How to create patterns for green sand technology: https://vietnamcastiron.com/sand-casting-pattern/
Pouring molten metal
Create two drag mold halves and cope mold by placing the drag pattern halves and cope pattern into the flask, fill the green sand and compact it.
Now we remove the pattern to create a kettlebell space inside the mold.
In the end just put the two flasks together and pour the molten metal into the mold. Air bubbles will be produced during the filling process and then escaped. If only one air bubble remains, the kettlebell surface can also be damaged.
Waiting 2- 3 hours for cooling, and then you just need to withdraw the mold and take the kettlebell casting out.
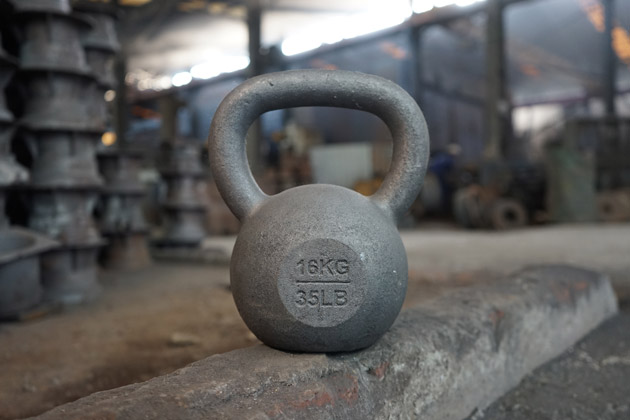
Both of the above molding technologies are applied by VIC to cast kettlebells and dumbbells. Depending on the needs of the customer, we will advise and give molding methods to produce products that are suitable for customers with the most reasonable price.
Surface finish treatment
The excess metals on the kettlebell will be cut by the cutting machine or smashed by the hammer . Then we will conduct grinding and machining to remove rough spots, excess edges for a more complete surface.
To launch kettlebell products with the smoothest and most perfect surface, we also use shot blasting machine to help kettlebell achieve the best finish.
Quality checks will be conducted such as weighing, shrinkage checks, defects, and errors arising in the casting process. If the product does not pass the quality test, it will be crushed and returned to the raw material.
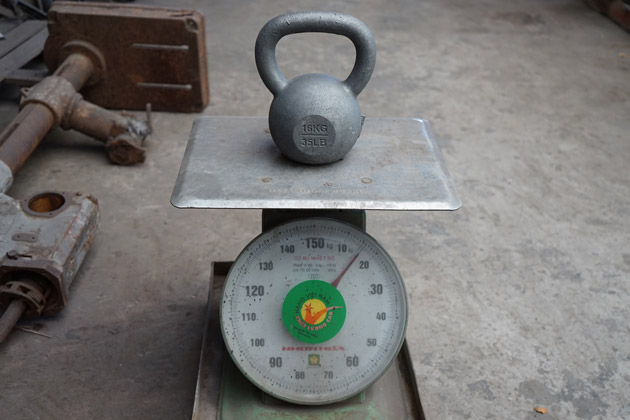
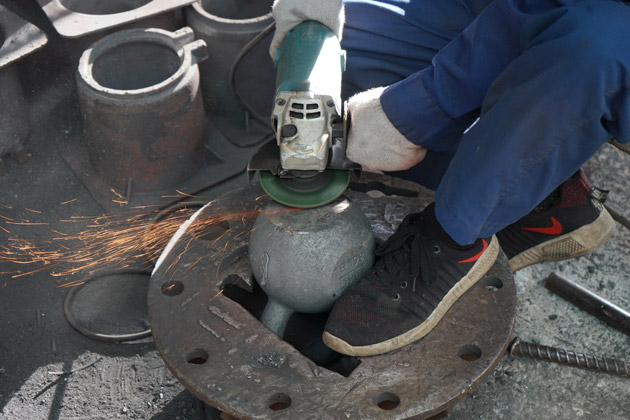
Powder coating
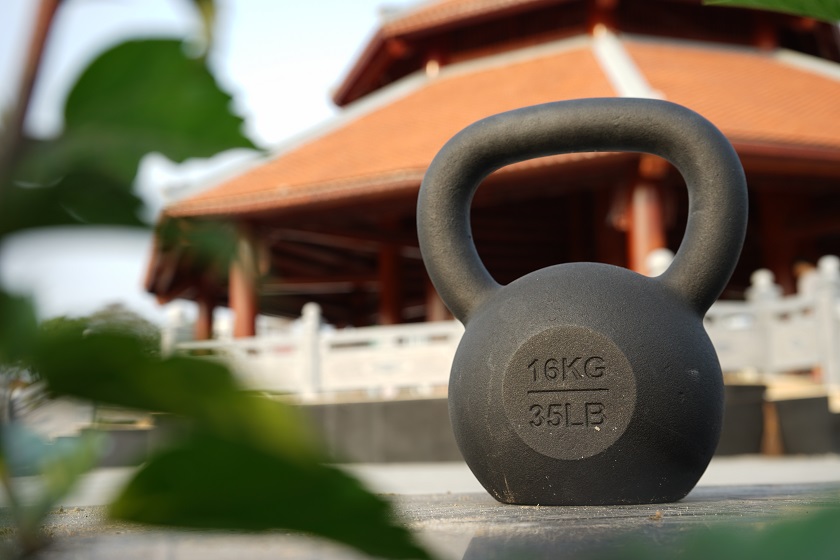
The kettlebell that you hold from VIC will be of much better quality than the ones you would see in the gym near your home.
A kettlebell is timeless, not only by the good material, but also by the coating.
The surface coating not only makes kettlebells resistant to corrosion and rust, but also increases grip on the handle so that athletes can perform their swing movements in the most natural form without worry being injured.
Here we apply the powder coating on the kettlebell surface finish. The surface after coating balances the smoothness and the good gripping feeling.
VIC Foundry information
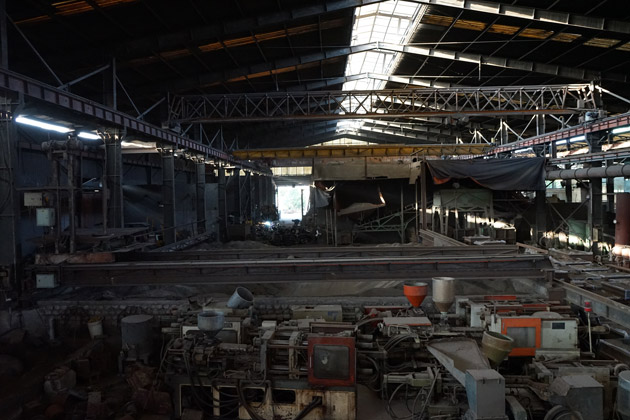
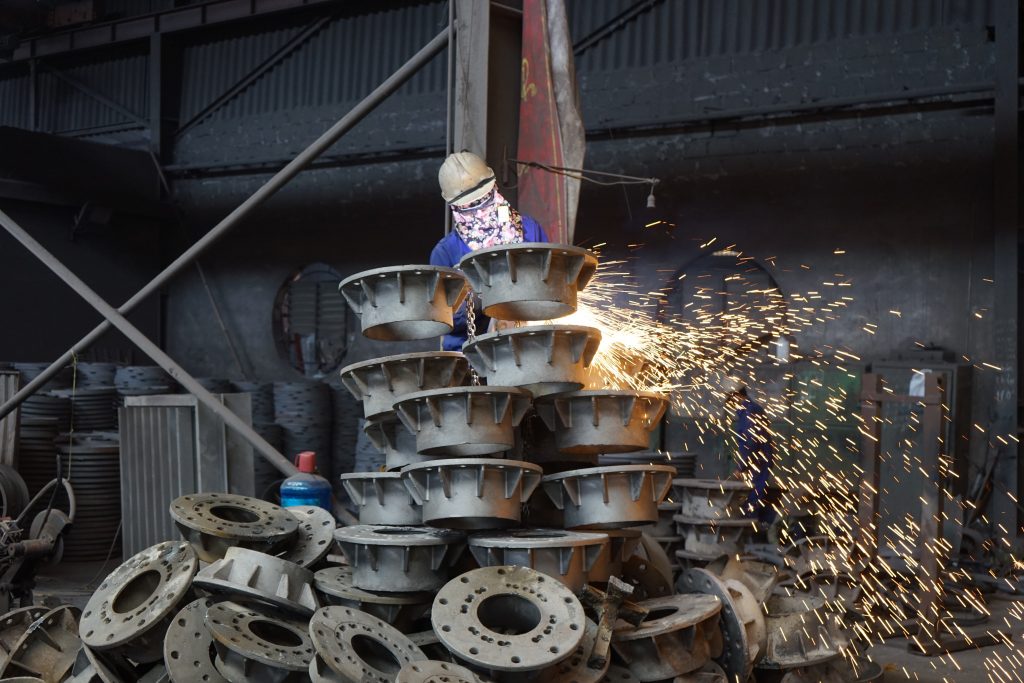
If you are looking for kettlebell manufacturers with good quality, reasonable price and responding to your order quickly, then it is VIC.
We are an OEM / ODM foundry, can advise on the best design for the customer. Or if you have the available drawings, do not hesitate to contact us and place a discussion.
Serving your kind request is our pleasure.
Serving your kind request is our pleasure.
Contact Information
Vietnam Cast iron Company Limited Contact
Address: Lai Xuan, Thuy Nguyen District, Hai Phong city, Vietnam
Phone: +84 86 543 0133
Email: [email protected]