Aluminum casting shrinkage is a big concern in the metalworking industry that every foundry has to tightly calculation to minimize casting defects and rejections. This article mainly focuses on analyzing shrinkage in aluminum sand casting that helps manufacturers predict and control shrinkage during the working process.
Sand casting is one of the most economic and popular techniques used to manufacture 1/3 casting parts across the world because of its efficiency and reclaimability.
Considered as a favorite molding treatment, however, the sand casting process exposes many defects which can cause casting rejections if you don’t manage the casting technique well.
One of the chronic issues in sand casting is shrinkage that required to calculate carefully to guarantee casting accuracy and quality.
Today, we discuss aluminum casting shrinkage during the sand casting process that is asked most of the time by readers.
You will find in this article’s content a deep discussion of the aluminum casting shrinkage phenomenon; helpful guidance to calculate aluminum shrinkage and techniques to control the shrinkage in sand casting.
What is aluminum casting shrinkage in sand casting?
Shrinkage is one of the characteristics of metals in the casting process. It is a normal phenomenon that metal shrinks as they solidify.
In aluminum sand casting, shrinkage happens when the molten aluminum alloy is poured into the mold cavity and cooled down. Shrinkage leads to internal or external changes of aluminum volume as it transforms from liquid to solid phase. In which, the specific volume of aluminum alloys is decreased when it turns from a liquid state to a solid-state.
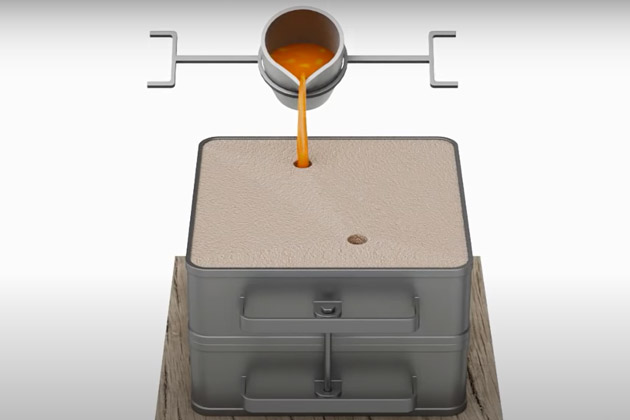
What is aluminum alloy casting shrinkage rate?
In casting, the shrinkage is calculated by the shrinkage rate represented by percentage (%).
Different aluminum alloys have different casting shrinkage rates. Even if the same alloy but the casting design is different, the shrinkage rate is also different. Generally, the shrinkage rate of aluminum alloys is ranging from 6 to 8% (specific amount depends on the specific alloy)
What influence of shrinkage on aluminum sand casting parts?
The aluminum casting shrinkage has a decisive influence on the quality of the aluminum casting parts. If the shrinkage allowance of aluminum in sand casting is not managed well, it can cause casting defects including open shrinkage defects (pipe and caved surface) and close shrinkage defects (micro-porosity or macro-porosity) that lower the casting quality.
What are the three steps in which aluminum shrinkage occurs?
As other metal, the aluminum casting shrinkage happens in three stages correspond with three types of shrinkage.
1. The Liquid Shrinkage
In an easy way to understand that liquid shrinkage is the shrinkage of the aluminum alloy liquid during cooling. Here the contraction occurs as the molten aluminum alloy cools but still remaining in the liquid form.
In casting, this stage of shrinkage doesn’t significantly effect on the designing perspective.
2. Solidification Shrinkage
Solidification shrinkage is the shrinkage of the aluminum alloy due to solidification. This phenomenon happens as the aluminum alloy transform from the liquid phase to the solid phase.
The shrinkage that occurs in this stage is because the liquid metal is less dense than the solid one. This shrinkage is the main cause of porosity as well as macrosegregation in aluminum casting parts.
This stage is where alloys shrink largest, hence it requires calculation of carefully supportive tools such as riser, chills to compensate for the alloy shrinkage rate.
You can find our guide on designing risers and chills on the rest of the article.
3. Patternmaker’s shrinkage
Patternmaker’s shrinkage is the continued shrinkage (after the solidification shrinkage stage) that occurred as the aluminum solid casting cools to room temperature.
This phenomenon happens because of the thermal contraction factor due to the temperature dependence of the solid density. This is the reason cause hot and cold cracks in aluminum parts that distort the casting shapes.
This shrinkage stage is also especially significant for design considerations. It requires the casting manufacturer to have to consider reasonable mold design and tool so that the final casting remains the desired dimension and accuracy.
You can find our guide on designing mold and tools on the rest of the article.
Which factors influence shrinkage in aluminum sand cast products?
There are several factors that affect on parameters of aluminum sand casting shrinkage including alloy composition, casting shape, pouring temperature, mold coat, thermal cooling conditions.
Let specify them!
1. Influence of Aluminum Alloy Composition
The composition of aluminum alloys has effects on the freezing range of metal and the shrinkage porosity formation as well.
Specifically, the long freezing aluminum alloys result to reduce the micro-porosity, and in oppositely.
Table of some of aluminum alloy freezing range
Alloy Grades | Composition | Approximate Freezing range (° C) | ||
150 | Al 99.5 | 657-650 | 7° C | Short freezing range |
A413 | Al –Si 12 | 575-565 | 10° C | Short freezing range |
A413 | Al-Si 12 Cu | 575-565 | 10° C | Short freezing range |
319 | Al-Si5Cu3 | 580-52 | 60° C | Long freezing range |
A356 | Al-Si7 Mg | 615-550 | 65° C | Long freezing range |
There are a range of Aluminum alloy types.
Among aluminum alloys, Al-Si is the most important alloy with about 60% casting parts because of its great casting characteristics and fine strength. The silicon element makes the iron softer that lower strength but decreases the aluminum casting shrinkage rate. Hence, the casting parts made of aluminum alloys groups of 3XX.X and 4XX.X are likely to be less shrinkage than other alloy series.
In additionally, alloys like titanium and zirconium that help to increase the fluidity also reduce the shrinkage parameter.
2. Influence of Casting Shape
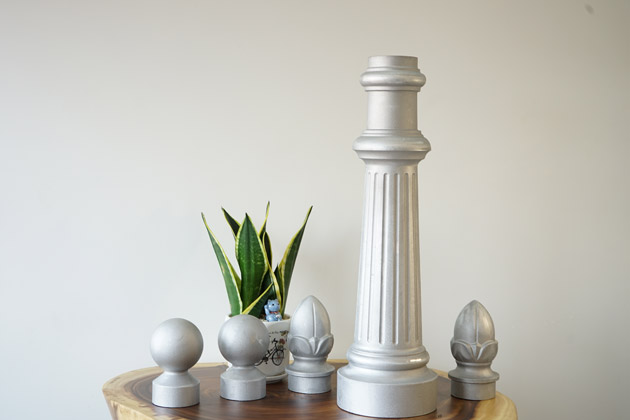
Another factor, casting shape has great effect on the shrinkage parameter of aluminum sand casting.
A lot of experimental researches have pointed out that, the shrinkage rate decrease in the flat aluminum casting and increases in the thick casting. This can be explained by the solidification behavior of the casting shape.
In casting, the edges cause heat extractions resulting in the casting shape plays a consideration in the solidification morphology of the casting in the localized areas.
Also, the shrinkage of complex casting parts with many details and edges are likely to be more shrinkage than the simple casting shapes.
3. Influence of Pouring Temperature
The pouring temperature is a vital factor that contributes to aluminum casting shrinkage. Add extra pouring temperature (or superheat) during the aluminum melting process can reduce the shrinkage rate of aluminum during sand casting and minimize the micro and macro porosities.
The additional pouring temperature plays the role of helping to increase the aluminum alloy fluidity, provide an allowance for heat losses before they are in mold cavity shape, and lower heat extraction rate by mold.
It is recommended to add T+ 50 ° C super heat to lower the shrinkage in aluminum alloys casting.
4. Influence of Mold Coat
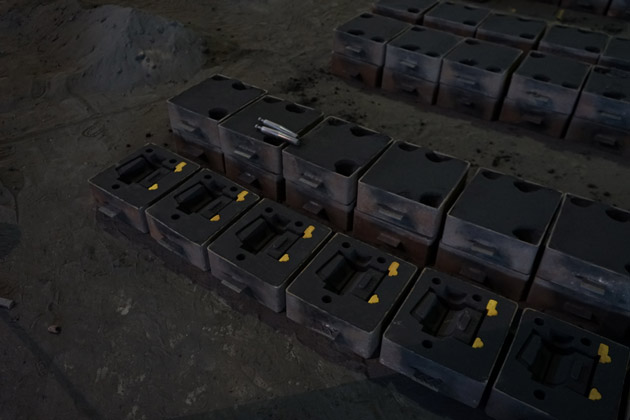
Apply several coating layers to the sand mold can help to reduce the aluminum casting shrinkage parameter.
The molding coat provides a smooth surface for the aluminum sand casting. By promote directional solidification, the mold coating affects the thermal gradient.
“Mold coat allows a passageway for feed metal to flow into the solidifying structure and compensates for normal metal shrinkage during solidification.”[1]
SAMAVEDAM SANTHI (2018)
Several layers of graphite coating to the sand mold before the pouring step is recommendable to reduce the casting shrinkage in sand-cast aluminum.
How to control sand aluminum casting shrinkage?
The three most important things you can intervene to control the aluminum alloy shrinkage as well as calculate shrinkage allowances are to design proper gating, feeder, and chills.
1. Design proper gating system
The gating system is the channel through which the molten metal flows to the mold cavity.
The gating system design has to ensure the continuous flow of the aluminum fluid.
The design of the gating system must ensure the criteria:
(1) Control the metal flow rate, not be impacted, not be swirled, not splashed, must be smooth and constant;
(2) Fills the mold cavity quickly without losing metal dilution;
(3) Controlling the temperature in the mold cavity to cool the metal stably.
Refer to a detail guidance on design gating system here.
2. Caculate Feeder (riser)
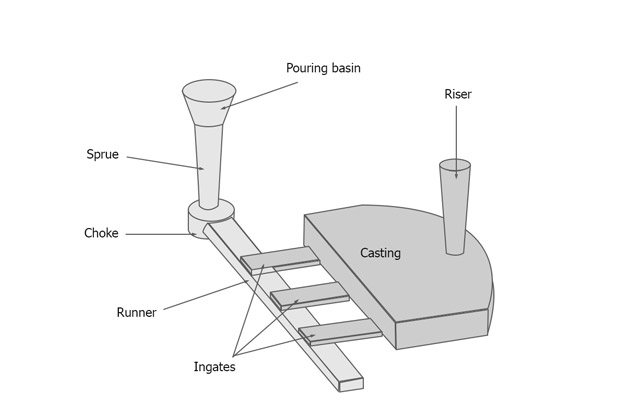
A feeder, also known as a riser, is a molten metal container in the mold, to provide fluid for the mold cavity in order to compensate for the shrinkage as the liquid cools.
Normally, with the complex aluminum casting parts, metal foundries often split the casting into different parts. Hence, feeders may also be placed in different areas.
An effective feeder has to be matched these two criteria:
- Contain enough molten metal to compensate the shrinkage
- Solidify later than the casting
How to calculate riser volume?
The riser volume is calculated by the formula: Vf ≈ αVc
In which:
- Vf is the riser volume
- Vc is cavity volume
- Α is shrinkage fraction
How to calculate solidification time?
According to criteria (2), you have to design a proper feeder, in which the solidification time of the feeder is longer than the casting solidification time.
Hence, it is required to calculate the solidification time of the casting, so that you can longer the solidification time of feeder.
The solidification time of the casting is calculated by formula: Tc= C.(V/A)2
In which:
- Tc is the solidification time of the casting
- C is a constant
- V is volume of the casting
- A is the cooling surface area
The ratio of the volume of the casting V to the cooling surface area A is called modulus M, which has a unit of length. The larger modulus M is, the longer the casting solidifies
By knowing the solidification time of the casting, you just need to make the modulus of the feeder Mf is higher than the modulus of the casting Mc.
But how much higher we should take? It is common calculate by 20% higher, in which Mf = Mc
How to calculate the maximum volume of the casting that can be fed from a feeder?
Additionally, the shape of the feeder also determines how much molten metal can be fed to the casting. According to some experimental research, a non-insulated cylindrical feeder only provides up to 14 % of its volume to feed the casting.
The maximum volume of the casting that can be fed from a feeder can be calculated by this formula: Vc= Vf. [(Vx– S)/S]
In which:
- Vc is the max volume of the casting that can be fed
- Vf is the volume of feeder
- Vx is the volume of metal available for feeding
- S is a volumetric contraction
3. Place Chills
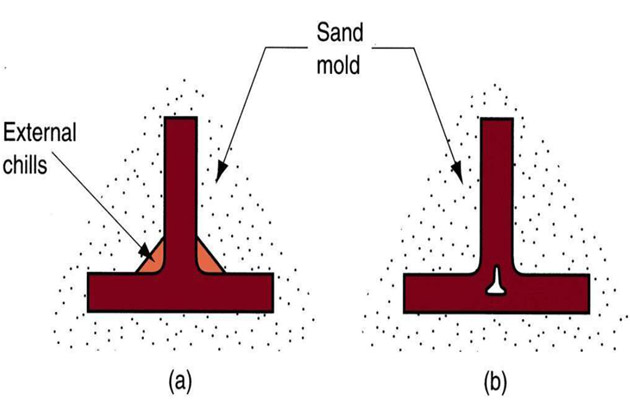
Another solution to address the aluminum casting shrinkage is to place chills. Chills are lumps of solid metal or graphite, inserted to assist feeders.
The chills are placed in strategic areas like thicker areas, heavier sections, etc.
Through increase the cooling rate in that strategic area, the chills reduce the ratio of the volume of the casting to the cooling surface area of the casting section.
To sum up
Shrinkage is a chronic consideration in aluminum sand casting that if the manufacturer doesn’t manage well can cause a lot of casting defects that lower the quality of aluminum casting parts.
Through the above content, we have provided suggestions on how to control the shrinkage in aluminum sand casting. Briefly summarize you can reduce the aluminum casting shrinkage by:
- Consider the aluminum alloys for the input material. In which, the Al-Si alloy series have the lower shrinkage parameter in comparing to other groups.
- Add extra pouring temperature or superheat during the melting process to increase the fluidity and to consider heat loss before they are in the mold cavity.
- Apply a coating layer to the sand mold.
- Design a proper gating system to ensure the molten metal flow continuously.
- Design a proper feeder to compensate enough for the shrinkage casting.
- Put chills to assist the feeder in the shrinkage compensation.
Hopefully, you will find useful information through our above content. Operation in the metalworking industry, our aluminum foundry specializes in providing casting solutions for a range of aluminum alloy casting parts.
Subscribe to our metal casting blog to get updates weekly relating to casting technique, casting process, advice solution, etc. Also, contact us if you are looking for an aluminum casting part manufacturer a supplier.
All the best wishes!
Read more:
How are kettlebells made by sand casting?
Aluminum casting methods: A comparision of process
———————————–
Reference
- Samavedam Santhi(2018).Calculation of Shrinkage of Sand Cast Aluminium Alloys. International Journal of Applied Engineering Research ISSN 0973-4562. 13(11).pp. 8889-8893. Available at https://www.ripublication.com/ijaer18/ijaerv13n11_19.pdf.
- Mark Jolly. Prof. John Campbell’s Ten Rules for Making Reliable Castings. Available at http://foundrygate.com/upload/artigos/YSi66RktqSYj7TZBzmEZ7FW6yQf8.pdf
Very well explain Sir…