Effective quality control is critical in manufacturing to ensure product quality, fulfill consumer expectations, and minimize the need for recalls. That’s why at VIC, we consider this process as an indispensable part of our production of any kettlebell lines. Let’s take a closer look at how we ensure to bring the best kettlebell product to our beloved clients!
If you work in the manufacturing industry, you understand how important it is to produce high-quality products while still sticking to deadlines and how much your customers expect the perfect-made package.
To balance and adapt to all of the above is not easy. If not adequately controlled, sometimes, the aim at producing the best-quality product might have a negative impact on deadlines; hence, customer satisfaction and your position in the market.
For this reason, the concept of quality control was established and became extremely favored all over the world.
What is Quality Control?
Despite the fact that everyone might have heard of this word, a straightforward and precise meaning would provide a better understanding.
Quality control in manufacturing is the process of making sure that each product follows pre-defined quality standards and is exactly what the producer and customer are looking for.
This also implies that any goods that fall short of the expectations will never be sold to the customer.
Though many manufacturers choose to inspect for defects at the end of a production cycle and when problems are spotted, corrections will be made immediately. Is that effective enough?
Of course not because when the product is finished, making any changes or repairs will result in massive waste on the part of the manufacturer, substantially increased associated costs, and a delay in delivery.
Rather than waiting for an entire batch of low-quality items to be manufactured and then inspected, we – VIC, adopts numerous inspections during the kettlebell manufacturing process to minimize liability risks, save time, resources, and contribute to the overall positive branding of our kettlebells.
CHECK HOW OUR KETTLEBELL LOOKS HERE!
Our Kettlebell Quality Control Process
To achieve the best result, we divide the kettlebell quality control process into several steps with the combination of Operators who control the production process and ensure minimal variation and Engineers who regularly monitor the product design for issues.
When a problem is detected, it will be fixed immediately.
1. First Check
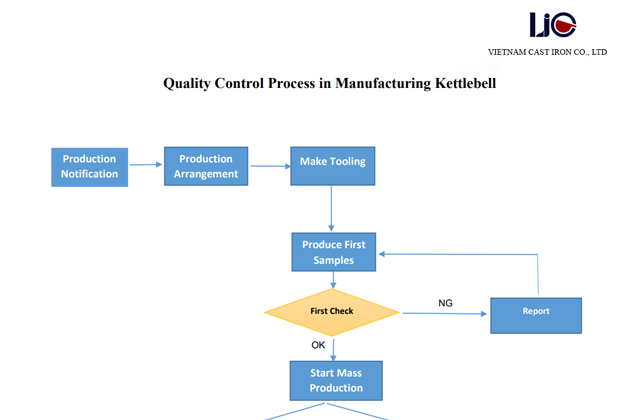
After the factory has finished producing the First Sample, the first inspection is performed.
Our foundry will arrange the required casting method and the production force as soon as we receive the production notification.
At the same time, the quality requirements for each product are also be established.
Check 5 things that must consider when checking kettlebell quality here!
Then we begin tooling and generate our first sample.
This sample will be tested right away to see whether it met the specifications that we – the manufacturer and the customer have addressed.
There are two possibilities: if the first sample is well-made, it will be sent directly to the production line for mass production; if it is not, we will recall the sample and rebuild a new version.
The ideal sample is essential in mass production because it influences both the finished product and consumer requirements.
Due to this step, VIC has the opportunity to minimize the risk of technical errors of the sample beforehand, resulting in products with the expected consistency.
Next, there will be a couple more quality checks during production regarding casting material and sand molding.
2. Incoming Quality Control
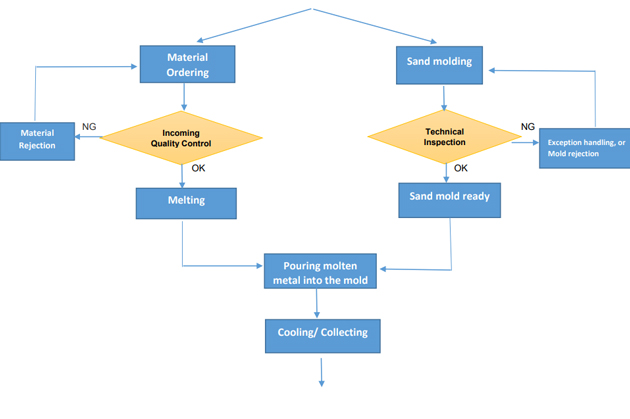
Before getting into bulk production, the quality of the material must be verified by composition analyze machines and our engineers.
Especially with kettlebell products, if a kettlebell is produced of low-quality materials, it will not be robust and can be easily damaged by a strong impact, which adversely affects the customer’s training experience.
Furthermore, the metal quality must be ensured to minimize the risk for the manufacturer, avoiding the case that the material used is of poor quality, leading to higher cost and time consuming for reproduction.
To achieve the best quality of the product, our regulations stipulate that only high-quality metals certified by validators can be sent to the melting stage.
3. Technical Inspection
In the meantime, we conduct another technical inspection on the sand mold, which is significant in forming a sand casting.
The composition and quality of the sand directly influence the final shape, dimensional accuracy, and surface finish of the finished product.
That’s the reason why this checking shouldn’t be overlooked.
The accepted and proper sand mold should be the one that can withstand high temperatures while retaining its shape, allow gasses to escape during the pour, easy to separate the sand from the casting at the end of the casting process, and should not react chemically with the metal.
Otherwise, it will be dealing by professionals or replaced by a better version.
4. Roughcasting Checking
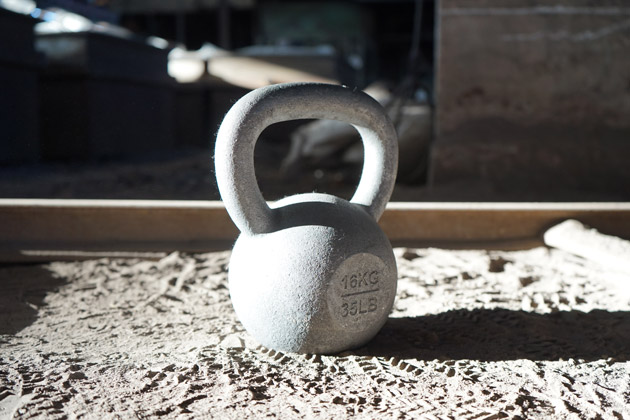
High-quality metal that is melted and poured into the sand mold produces the roughcasting product, and it will be checked by our technical team.
The inspection will evaluate every aspect of the kettlebell, from the sturdiness of handle, handle width, base, weight, surface, etc., to determine whether this kettlebell is ready for the next step: Painting.
If anything goes wrong, procedures for handling defects will be implemented right away, or the unacceptable product will likely be eliminated.
Read more about How our kettlebells are made?
5. Full Inspection
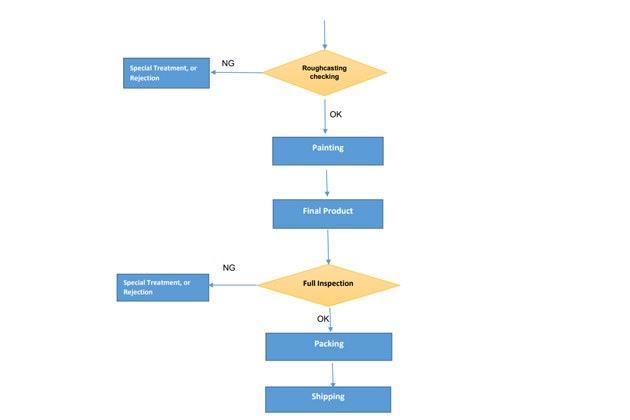
Let’s come to the final checking! After being perfectly finished and machined with a smooth surface, sturdy handle, and polished paint finish, the kettlebell product will be considered to be the end-product and will only be packaged and delivered to the customer if it passed the final inspection.
Here, further testing and potential repair work will be conducted by experts who will re-evaluate the entire finished product, including construction, surface finish, size, material, and so on, to ascertain if the product meets the defined standard or it needs to be taken to further processing.
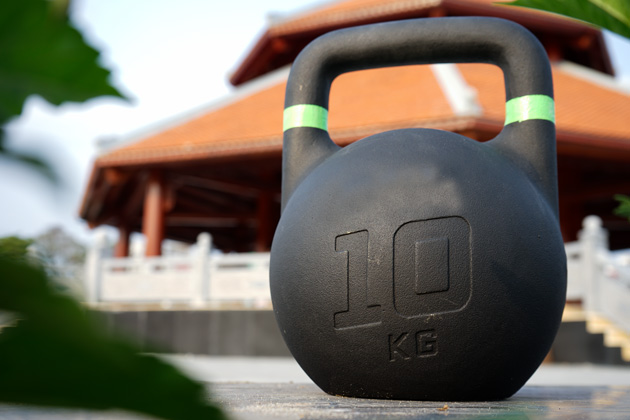
These steps are the synthesis of inspection so that once again, we assure the quality of our product before shipping to customers. Plus, to handle any issues that arise in a timely manner.
——————————–
Explore more:
Is it worth buying cheap kettlebell?
Vinyl Kettlebells Vs Powder Coated Kettlebell: Which one to buy?