The metal foundry is the facility that works on manufacturing the metal casting product by pouring the molten metal into the mold. It provides the casting parts and servers almost industry in life.
If you spend time to notice you may happen to aware that so many of the items surrounding us are from a metal casting foundry somewhere. Have you wondered how they manufacture excellent cast aluminum lamp post standing charmingly on the roadside or by what manner super detail cast iron machine parts are created?
From marine, urban outdoor furniture, transportation to agriculture machinery, construction industry we all see the casting products of the metal casting foundry. Its application presents popularly surrounds our daily life but most of us are next to know nothing about this metalworking industry.
Today’s article, VIC brings to our beloved readers a summary of how the metal foundry work? Hopefully, you will find interesting facts relating to the metal casting industry through our post.
What is a metal foundry?
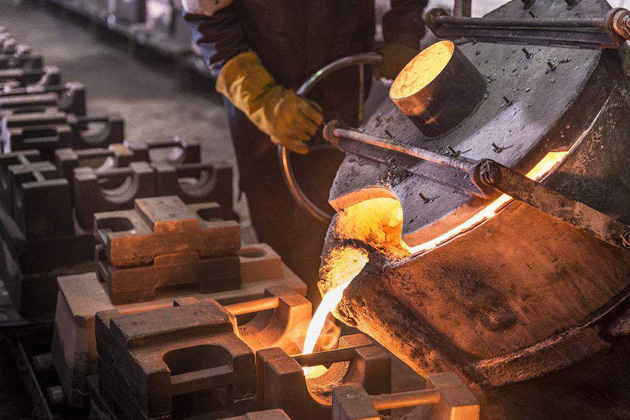
Well, a metal foundry, simply explained is a facility that works on metal casting to provide casting parts in different shapes and designs as required.
The metal casting foundry today serves a range of industries. Its work closely corresponds to tremendous fields such as transportation, lighting, urban furniture, machine, marine, construction that related to numerous of the essential consumer products we depend on.
The metal casting industry is very large, hence foundry metal is also various dividing on the focused working field, metal, etc. There are foundries that mainly work on cast iron or cast aluminum for example; a range of facilities specialize in machine parts; street furniture, home cookware, OEM, so on.
Which metal is used in the foundry?
The casting foundry mainly works on different metal materials, mostly are cast iron, aluminum, bronze, steel,and brass.
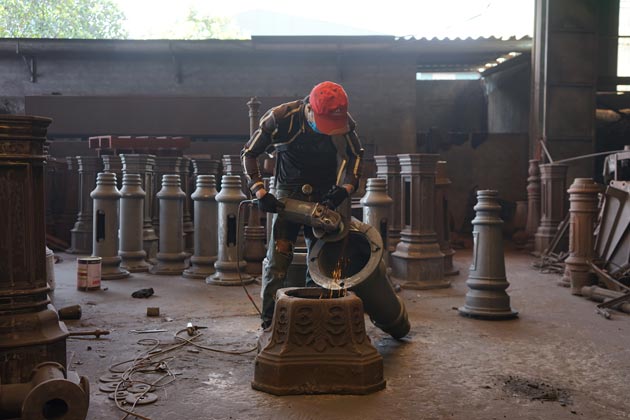
Each metal does not maintain similar casting properties and it is very important to consider very carefully which material is suited to each industrial product.
Aluminum is preferentially treated as a good cast-ability material. Its low melting point (approximately 660°C) allows saving time in comparison with other metals (bronze at 950°C, cast iron at 1100-1900°C of cast iron for example).
Furthermore, aluminum’s versatility also allows casting different shapes and styles therefore it is applied widely in many industries from outdoor street furniture to machine parts. The collected aluminum casting parts are highly appreciated for their smooth, polished, and bright surface finish.
At the same time, cast iron is often seen in manufacturing lighting post base, agricultural counterweight, urn planter, manhole cover, bollard, etc. due to its high-density weight and long-lasting with external expose. Cast iron lighting pole can stand at least 50 years and face up with extreme weather but still performs good look, whereas, the ductile iron manhole cover is able to withstand a dozen tons of loading.
Oppositely, steel material is easy to get rust so it is limited to use for outdoor application or requires further expensive treatments if in need.
What is the metal casting process in the foundry?
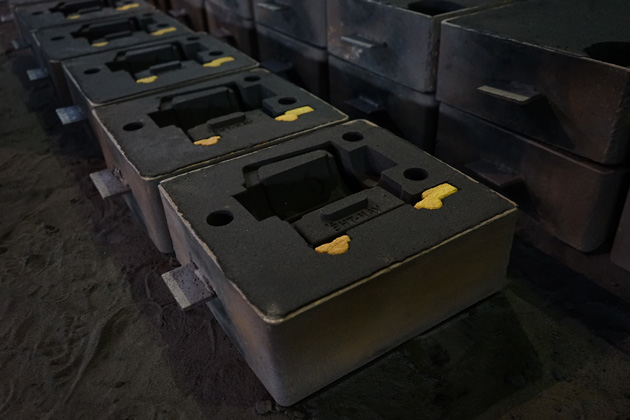
By definition, you may think it is just a piece of cake but once you step into a certain foundry nearby you will know how skillful and ingenious this casting work is. Casting any product in a foundry all involves many steps and each step requires careful and exactly working spirit.
Summarized speaking, the general metal casting process involves pattern making, molding, pouring, cooling, shaking-out, sand-blasting, fettling, and inspection. The further machining step applied CNC precise machine for milling, turning, lathe etc. is upon request and depends on each foundry’s capacity.
In the first step, pattern making is very important in the metal casting process. The pattern is a replica of the project to be cast. It is commonly made from wooden or metal (aluminum is widely used). These patterns can be reused to create as much mold cavity as needed.
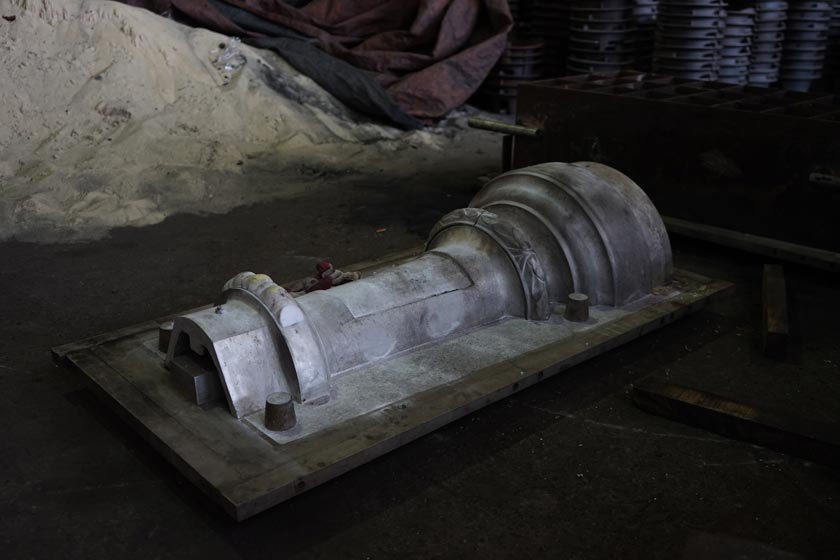
Among the molding techniques, sand molding seems like the most favorite and widely applied molding process in the foundry due to its low cost. The sand mold technology can apply for either small and large foundries; and is very easy to process in comparison to other manners.
In the sand molding technique, green sand is most commonly features wet-content and naturally high bonding ability. Basically, the worker presses the pattern into the sand flask and the mold cavity is created after the pattern withdrawing. This step can do either by automatic line or manual.
The cavity features the shapes as the pattern does and includes a few holes and lines for the pouring step. By pouring the molten metal into these cavities, the casting is formed. Nowadays, melting metal mostly is processed by an electric furnace, whereas coal furnace can find in a few small foundries.
After pouring, it requires a few hours to allow the casting to be cool down. Roughcasting is collected by the shaking-out process and goes through cleaning remain sand.
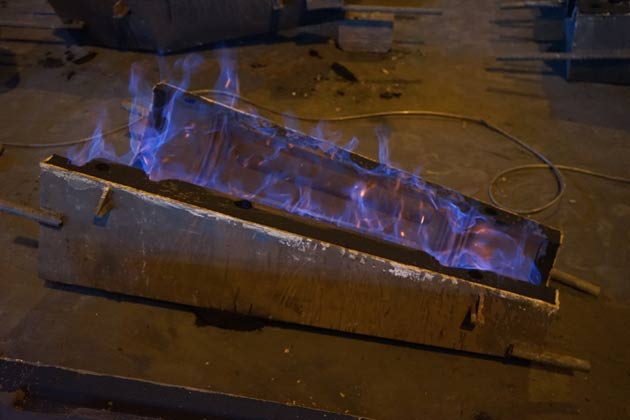
Depending on requirements, the fettling can be simple, complicated, and hard work. It could be applied treatments for surface defects such as pinhole, crack, rough skin, etc. The inspection will be carefully processed before shipping to the customer.
Which equipment included in the casting metal foundry?
Large-sized casting metal foundries are mechanized heavily. They equip all the machinery and equipment for almost processes such as pattern making, molding, pouring, cleaning, machining, etc. That modern metal casting foundry includes high advance machining machines, high capacity furnace, automatic line, forklift, crane, conveyor, assistant robot, etc.
CNC pattern making machine in foundry Cutting machine uses in the metal casting foundry
Small to medium metal casting foundry works based on either semi-automatic or manual process, but the furnace and molding lines are essential.
The furnace used to melt the metal is various depending on capacity and fuel. The traditional furnace includes the coal furnace and the electric furnace. More advanced type names electric arc furnace (EAF), induction furnace, cupolas, and reverberatory. The furnace can range in size, from tabletop type to equipment that weighs several tons. The bigger furnace is, the higher the melting capacity it performs.
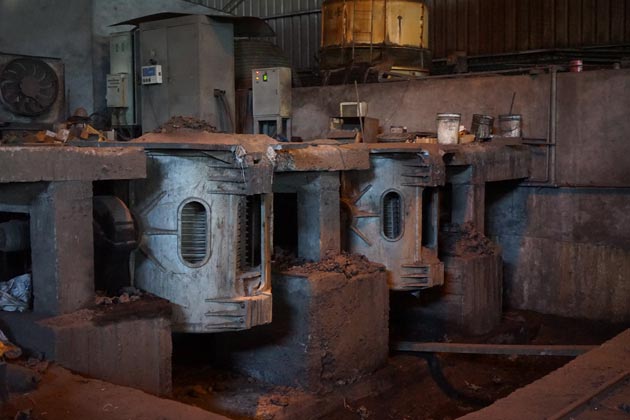
Molding line, another very significant to any casting metal foundry. Each molding technique requires a distinct manufacturing line equipped with supporting equipment. There is its own line for the green sand casting process, similar to furan resin sand casting, lost foam casting.
How to ensure safeness in the metal foundry?
Obviously, metalworking is such a heavy industry and maintains many unexpected hazards. The violent and unpredictable nature of the chemical reaction is always concerned. Hence, it is vitally important to take the safeness of workers into the account.
Ensuring labor safety in the metal casting process to minimize injuries and accidents to workers, to avoid loss and damage to people and property for the foundry. Prior to run the operation, any metal casting foundries have to guarantee safety protocols regulated by the authority.
The metal foundry design and equipment used are required to ensure safety with the worker and nearby areas.
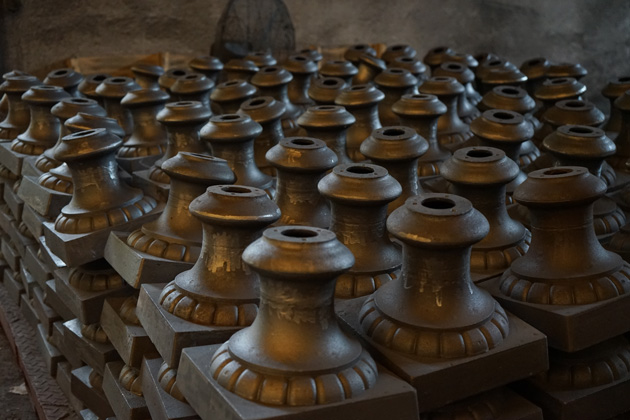
Unsurprisingly, the metal foundry temperature is very hot. It daily works with melting metal that could heat up to 2000oC. In this working condition, the roof has to be high to allow air circulation. It better should be constructed of non-reactive, flame-retardant materials. It is also recommended to invest in mechanical supports such as forklifts, mechanical ladles, or conveyors to minimize human exposure and reduce the hazard counter.
The worker in the casting foundry has to been equipped with protective clothing fully such as a hat, eyes cover, glove, and so on depending on each working position. To prevent unexpected accidents, fire and explosion-proof equipment have to be always ready.
Also regularly check the machine, automatic line, furnace, etc. to find out failure, electricity leakage, or incorrect operation if there are any is needed. The worker also is asked to compliance the standards and procedures for using the machine safely.
Additionally, the metalworking foundry also has to ensure other external conditions such as providing enough lighting, ventilator, or control noise, etc.
Which industry does the metal foundry serve?
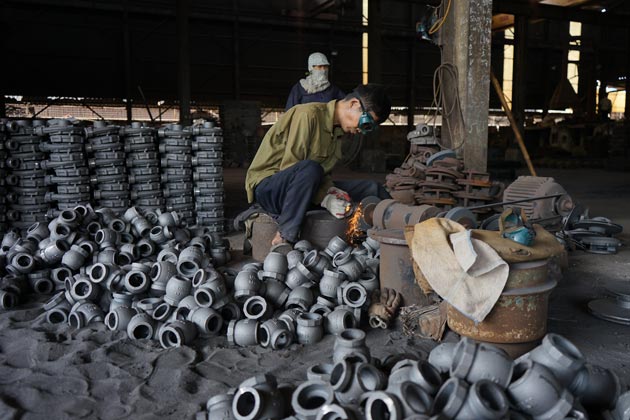
Currently, the market demand for casting products is huge. From agricultural machinery, construction machinery, industrial equipment, transportation, marine, water supply and drainage, urban decoration, electricity, metallurgy, mechanics, and so on, all use casting parts from the metal foundry.
It is very common to catch outdoor lampposts in front of your yard or along the street to your office. This lighting fixture is mainly manufactured by casting technique and constructed of metal material (cast iron and cast aluminum are mostly preferable). Similar to street furniture such as manhole covers, bench ends, litter bin, fence, railing, or kitchen equipment as gas stove accessories, cookware.
Machinery for agricultural, industrial, defense, aviation, marine…also no longer to skip from casting details.
VIC is proud to inherit the traditional casting profession from our great grandfather and deliveries the best metal casting product to the world market. We are the OEM and ODM metal casting foundry specializing in casting customized products upon different requirements. Kindly suggested checking our casting blog to get to know more about the metal casting techniques. Also, contact us if you are looking for a reliable and reputable metal foundry for your project.