Aluminum casting temperature has great effects on the aluminum alloy mechanical properties as well as determines the quality of aluminum casting parts. The article analyzes its two main parameters including melting temperature and pouring temperature of aluminum in the sand casting process and specifies the optimal temperature to fabricate the best aluminum casting quality pieces.
As one of the third largest abundant elements on the Earth, aluminum casting has a wide range of applications in both industrial and non-industrial fields, from automotive, transportation, building, outdoor furniture, aviation, to kitchen accessories.
As the world need tends to require high precise details and fewer casting defects, it is called for aluminum foundries have to control and calculate tightly the technical related issues to manufacture good casting products that match customer requirements.
Aluminum casting is defined as the process of melting aluminum alloys, pouring the molten aluminum into the molds, and cooling. In which, specific aluminum casting temperature including melting temperature and pouring temperature is one of the topmost vital factors that directly and indirectly affect the final aluminum casting quality.
Hence, it is crucial to well aware of the melting and pouring temperature of the aluminum alloys that you want to melt and cast.
In that article, we will help you clear these considerations.
- Aluminum Melting Temperature
- Effects of Aluminum Melting Temperature on the Casting Quality
- Pure Aluminum Melting Temperature
- Melting Temperature Range of Aluminum Alloys
- Aluminum Pouring Temperature
- Effects of Aluminum Pouring Temperature on the Casting Quality
- Calculate Aluminum Alloy Pouring Temperature
- Aluminum Pouring Speed
- Conclusion
Aluminum Melting Temperature
Effects of Aluminum Melting Temperature on the Casting Quality
As one of two aluminum casting temperature parameters, the melting temperature has a great effect resulting the quality of aluminum casting parts.
The melting temperature provided to liquidfy metal has to be sufficient, not too low, and not too high to obtain the best casting quality.
If the aluminum melting temperature is not sufficient (low melting temperature) can result in casting defects like aluminum casting shrinkage because the fluid is solidified before it is filled to the mold cavity.
Oppositely, if the aluminum melting temperature is excessive (high melting temperature) can cause the presence of hot cracks in the molds and lately formation of porosities in the casting parts.
Therefore, it is required casters to calculate the exact melting temperature range of aluminum in used not only to ensure the input material quality but also to calculate the proper pouring temperature later.
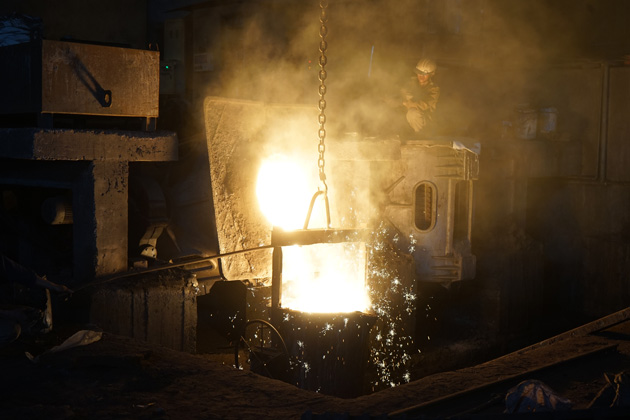
Pure Aluminum Melting Temperature
The melting temperature of metal depends on its purity. It is applied to specify aluminum melting temperature too.
As cited on many researches, pure aluminum comes in some specific types depending on the content of aluminum.
Particularly, the melting temperature of three pure aluminum types showed as the table 1:
Table 1: The melting temperature of some pure aluminum
STT | Type | % of aluminum content | Melting temperature (° C) |
1 | Ultrapure aluminum | 99996% | 660,37 °C |
2 | High pure aluminum | 99,5 % | 657 °C |
1 | Pure aluminum | 99,0 % | 643 °C |
Melting Temperature Range of Aluminum Alloys
Since the mechanical performance of pure aluminum is low, the aluminum material used for casting is alloyed with other elements such as Silicon, Copper, and Magnesium to increase its cast-ability, corrosion resistance, strength, and mechanical performance for these above uses.
Aluminum alloys come in a series of types corresponding with its alloy ranges.
Aluminum alloys don’t liquidify at a specific melting temperature but it comes in a range of temperatures that depending on the alloy composition.
Generally, adding alloys reduce the melting temperature of aluminum. Aluminum alloy melting temperature comes in the range of 463 –to 671° C (865-1240°F).
Refer to the melting temperature ranges of some common cast aluminum alloys designed as Aluminum Association (AA) System on the table 2.
Table 2: The melting temperature range of some common cast aluminum alloys (AA designation)
STT | Aluminum types | Melting temperature range |
1 | 150 | 657 °C |
2 | A356 | 557.2 – 612.8 °C |
3 | A380 | 566°C-580 °C |
4 | A413 | 649 – 760 °C |
5 | A360 | 577°C-612 °C |
6 | 319 | 516 – 604 °C |
7 | 390 | 507 – 649 °C |
Aluminum Pouring Temperature
In the aluminum casting process, the molten aluminum has to ensure to be poured eventually into the mold cavity through the gating system and flow to full fill all the mold cavities and edges before the metal freezes.
One of the vital parameters that influence this process is pouring temperature (to be analyzed here), and another is pouring speed (will be discussed in the next section).
Effects of Aluminum Pouring Temperature on the Casting Quality
Aluminum pouring temperature, together with the melting temperature, is the aluminum casting temperature parameters that much influence the mechanical properties and casting-ability of aluminum alloys.
Similar to melting temperature, the aluminum pouring temperature has to be provided sufficient, not too much, not too low to ensure the casting part quality.
Adding too high pouring temperature can cause shrinkage, mold wrapping and reduce the dimensional accuracy of the aluminum casting products.
On the other hand, the too low aluminum pouring temperature can result in the mold cavity is not fully filled due to the rapid solidification of aluminum alloys, causing casting defects and inaccuracy.
Additionally, it has been observed that pinholes in aluminum casting parts are formed due to the absorbed hydrogen. By providing an adequate pouring temperature to aluminum alloys, it helps to reduce the porosity created during the casting process.
Calculate Aluminum Alloy Pouring Temperature
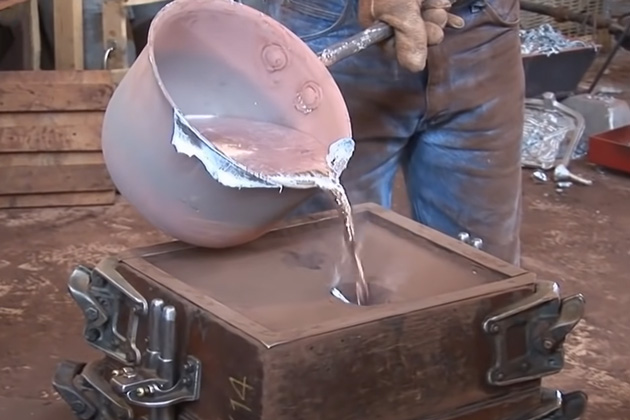
The aluminum alloy pouring temperature requires to be higher than the melting point.
Add extra temperature (superheat) during the aluminum alloy melting process helps to increase the fluidity, compensate the heat losses before they are in the mold cavity shape, and lower the heat extraction rate by mold.
It has observed that the optimal pouring temperature range of aluminum alloys are 680°C to 750°C.
At this range, the aluminum casting parts are produced with good mechanical properties and casting quality.
And the best pouring temperature to aluminum alloys to obtain the best surface finish of aluminum casting products has to be tested in the range of 680°C – 700°C.
At a higher pouring temperature, it will obtain the very rough casting surfaces, lower the strength of casting, and trap gases causing casting defects such as blowholes.
The effects of mold design on aluminum pouring temperature
Moreover, the pouring temperature of aluminum alloys is also partially influenced by the different mold sizes and capacities relating to the wall thickness of the casting.
Accordingly, a higher pouring temperature is applied for thin wall aluminum casting parts, whereas, a lower pouring temperature is usually used for thick wall castings or solid pieces.
Refer to Handbook of foundry practice, Fachverlag Schiele & Schön, Berlin, it recommends that thick-walled casting parts are preferred to pour between 620°C while the thin-walled design should be poured at up to 730°C.
Aluminum Pouring Speed
Besides the pouring temperature and melting, it is very necessary to take the pouring speed of aluminum alloys into account to obtain the best casting parts.
At the different pouring rates, the casting outcomes perform the different perfections.
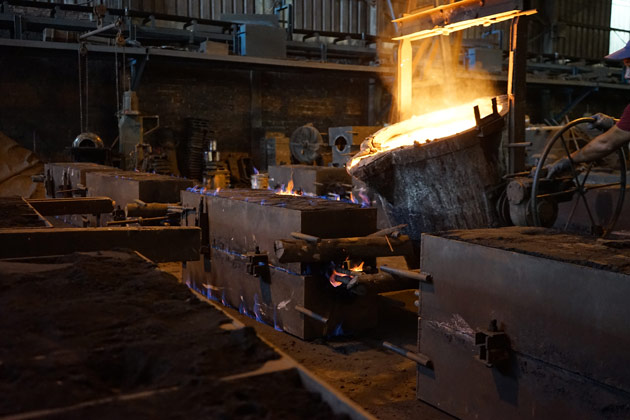
Effects of Aluminum Pouring Speed on Casting Part Quality
The aluminum pouring speed has great effects on final casting quality. It requires to be poured at an adequate speed to maintain the best casting outcome.
Accordingly, if the molten aluminum is poured at a too slow speed, the fluid will not fill all the mold cavities and corners because of a lack of pressure and solidification.
Oppositely, if the pouring speed is too quickly, it will create the possibility of turbulence that results in casting defects in aluminum casting products such as inclusions, dross, gas holes.
Calculate Aluminum Pouring Speed
Pouring speed defined as the flow of the metal per unit time.
The pouring speed of aluminum V is calculated by the distance of the ladle above the pouring basin per unit time of pouring the metal.
Its formula is expressed as: V = H / T
In which:
- V is the pouring speed (cm/s)
- H is the height of the ladle above the pouring basin (cm)
- T is time for pouring the molten metal (sec)
The optimal pouring speed to aluminum alloys has to be observed in range of 2.2 – 2.8cm/s.
At this pouring rate range, the aluminum hardness, tensile strength and deformations are obtained at the best performance.
Specifically, at the range of 2.0cm/s – 2.7cm/s, the final casting parts are collected at the best surface finish. Also, the perfect degree of aluminum casting surface finish is reduced as the speed increases.
The effects of casting shape on aluminum pouring speed
The density of the aluminum casting is a vital consideration in the pouring process that determines the pouring rate.
Accordingly, with respect to the thin-walled casting parts, the pouring speed is required to be carried out faster than for thicker casting parts so that the aluminum fluid does not chill.
Conclusion
It has been demonstrated that the aluminum melting and pouring condition has great effects directly or indirectly on the mechanical performance and final casting part quality.
Therefore, the casting process of aluminum parts required a lot of skills and expertise of foundry casters to proper calculate the adequate aluminum casting temperature so that manufacture high precise and accuracy casting products meeting customer requirements.
Through the above content, we have provide a concise discussion on the effects of melting temperature, pouring temperature and pouring speed to the aluminum outcome, together with optimal values of these parameters. Hopefully, it will be a helpful reference for your foundry practices.
Don’t hesitate to leave a comment to distribute your knowledge on our discussion. We welcome all the goodwill contribution and sharing.
Reference
Ager P, Iortsor A, Obotu GM. Behavior of Aluminum Alloy Castings under Different Pouring Temperatures and Speeds. Discovery, 2014, 22(74), 62-71.
Read more about A comparison of differnet aluminum casting methods
Temperature range with respect to wall thickness to be defined for best pouring activities .