Working in a foundry, definitely there are many harmful factors such as fine dust, toxic gases, noise, temperature, splashing molten metal, etc. If these hazards are not tightly controlled or prevented, they can threaten seriously the foundry worker health as well as working effectiveness.
In this article, we sort out hazards of working in a foundry plus preventive measures as well as how to handle these problems to ensure foundry safety and worker health. Let’s check together with VIC.
- 1. Dust in foundry
- What causes dust in the foundry?
- How hazardous dust in the foundry is?
- How to prevent and reduce risks of dust exposure at the foundry?
- 2. Gases, vapors in foundry
- 3. Hazardous noise in foundry
- 4. Vibration hazard in foundry
- 5. Heat stress in foundry
- 6. Toxic chemicals in foundry
- 7. Explosion in foundry
- 8. Other injury in the foundry
- Causes of physical injury in the foundry
- Common physical accidents:
- How to prevent and minimize risks of accidents in the foundry?
- Conclusion
Dangerous hazards at a foundry
1. Dust in foundry
One of visible foundry employees hazards come from dust. The foundry dust is formed during most stages of the casting process. The main composition of dust in the casting foundry is SiO2. The dust presenting in the foundry environment has a silica concentration that freely varies with the dust control process and the chemical composition of the sand.
The process that generates the most dust is the sand preparation step to make molds and cores. The dust composition depends on the binder used.
According to the US Occupational Safety and Health Administration (OSHA), the total amount of silica dust in the air at the new PEL level is 50 µg/m3 over eight working hours. The total amount of dust consists of particles, ranging in different sizes from nature or generated during working processes.
Compound | PEL (OSHA) |
Total dust | 15 mg/m3 |
Respirable dust | 5 mg/m3 |
Inhalable dust | – |
Silica dust | 50 µg/m3 |
Control dust is strongly important in ensuring foundry safety and it is required to keep that the total amount of dust does not exceed the OSHA exposure limit for the silica dust.
PEL has been determined by OSHA to be nearly undetectable with modern sensors. Even though dust is invisible in the air by naked eyes, the dust concentration may still exceed the limit and affect foundry worker health.
What causes dust in the foundry?
- Dust is generated from quartz in the sand during the mixing, casting and shaking process.
- The sand conditioning process for reuse also generates dust. Reusable sand is added with water and binder.
- At the sand mill stage in the molding step, or sand shaking when removing the mold creates dry sand, which is much more dangerous than wet sand.
- Dust is also generated when using the shot blasting machine to smooth the surface of the casting. Dust contains many toxic metals and free silica.
- During the metal melting process, smog is also formed. Smoke dust from the kiln is extremely fine dust with very high SiO2 and Fe content. Most commonly used metal furnaces in a foundry include: Crucible furnace, cupola furnace, and electric arc furnace. In which the cupola is the furnace that generates the most smoke.
- In addition to silica, dust can also arise from chromite or olivine sand.
How hazardous dust in the foundry is?
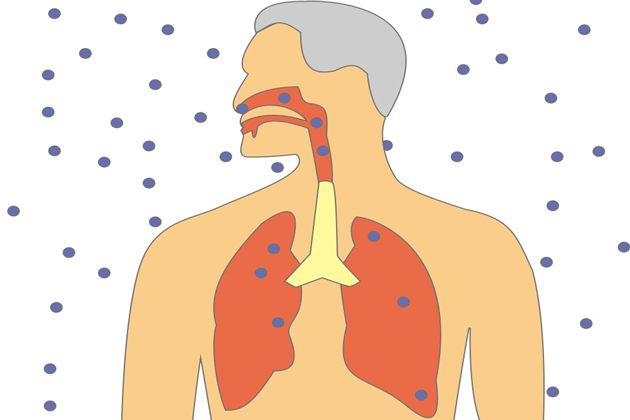
- If the worker in the foundry is exposed to high concentrations of silica it can cause lung-related diseases such as bronchitis, tuberculosis, lung disease silicosis and other complications. If long-term exposure, there is a risk of lung cancer.
- With unfiltered sand, silica crystals can form scar tissue in the lungs that interferes with lung function.
- Metal dust can cling to electrical equipment and catch fire causing problems with fire, explosion or short circuit.
- In particular, smoking in the foundry also causes resonant effects with silica dust that directly affects health.
How to prevent and reduce risks of dust exposure at the foundry?
- Install local exhaust ventilation system in stages causing high dust pollution such as mixing or grinding dry sand, shake out …
- Add personal respiratory protection equipment such as respirators, specialized masks in case the ventilation system in the foundry is not enough to remove dust in those areas.
- Avoid using sand with moisture below 2%, should use more binder to reduce the amount of loose sand.
- Use an efficient dust collection system (eg CMAXX).
2. Gases, vapors in foundry
In the foundry work, pollutants exist in the form of gases or vapors. These substances are produced during the casting process, including carbon monoxide, formaldehyde, phenol, isocyanate, isopropyl alcohol, etc.
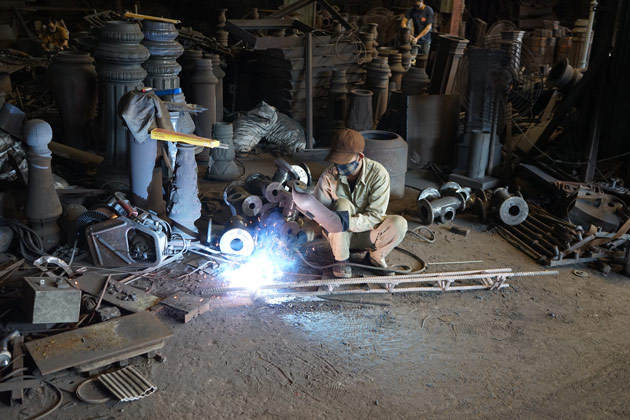
Carbon monoxide
Carbon monoxide (CO) is a gas produced from metal furnaces and during metal pouring into mold process. CO is colorless, odorless, and has no specific warning properties. Hence, air concentration should be monitored regularly to determine CO levels.
How harmful CO gas is?
- Foundry worker inhales CO resulting blood being prevented from supplying oxygen and causing suffocation.
- If exposed to CO 500-1000ppm for about 30 minutes, it can cause headaches, tinnitus, dizziness, nausea, and mental confusion. Exposure above 1000ppm can cause fainting, and even more severe it can lead to death.
How to prevent and minimize CO exposure?
- Install exhaust ventilation to control CO emissions.
- Foundry worker working in areas with possible CO exposure must be instructed about the dangers, how to recognize and how to treat CO poisoning to ensure foundry safety. It is recommend to check CO levels in blood or breathing of workers regularly at the end of working shifts.
Metal fumes
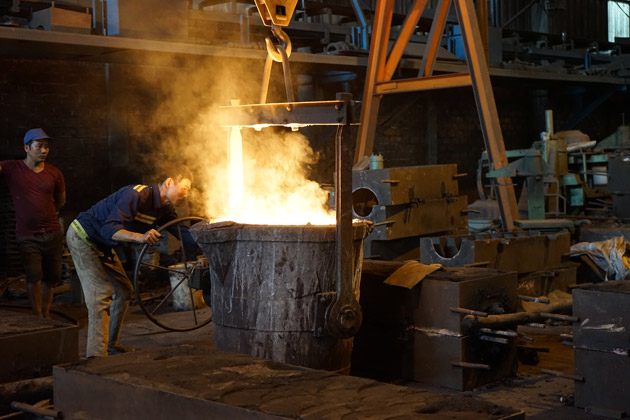
Metal fumes are produced during the melting, pouring and welding foundry work process. In ferrous metal foundry workshops, the fumes of lead, magnesium, zinc, nickel, chromium, copper, aluminum, cadmium, antimony, tin, and beryllium may be generated. Particularly, iron and steel foundries will be more likely to generate Fe2O3 smoke.
Especially leaded metals, the casting or melting process will lead to generate large amounts of lead fume emissions known as dangers of melting lead.
Moreover, with oven cleaning step, waste removal and lead alloy collection also pose a risk of lead contamination.
How harmful metal fume is?
Inhalation of metal fumes (especially zinc) can cause metal fume fever and eye irrigation that seen as common foundry health hazards. Symptoms that appear 2-10 hours later are nausea, headache, dry throat, wheezing, chills, chest pain, and often mistaken for bronchitis or pneumonia.
In-depth diagnosis is increased white blood cell count; increased skin metal concentration and blood count. Abnormal signs also appear on X-ray.
How to cure metal fume fever?
Ask the patient to lie down and drink enough water, and use symptomatic therapies such as aspirin to relieve headache symptoms. Metal fume fever usually clears up after 24-48 hours of expose treatment.
Toxic vapors
The use of wood or plastic as patterns in sand casting will produce toxic fumes that cause asthma and allergies that worsen foundry worker health.
How to prevent and minimize risks of metal fume and posion gas exposure?
- Install the air inlet above the metal furnace to suck the fumes and lead them to the exhaust gas control system.
- Need to collect toxic vapors generated from the emission point and properly treat.
- Carry out air testing where necessary to ensure the pollution concentrations do not exceed Workplace exposure standards for airborne contaminants.
- Use foundry safety gear in case other control measures are not feasible or to increase worker protection from foundry employees hazards as well as ensure foundry safety. – Consider alternatives to less toxic substances, or modify procedures to minimize the generation of toxic fumes and vapors
3. Hazardous noise in foundry
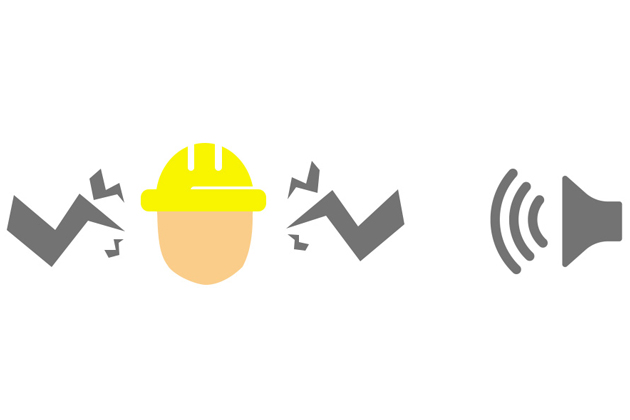
Hazardous noise is noise that exceeds the standards for workplace noise exposure. Standard for continuous noise exposure is 86 dBA for 8 working hours.
Metal is an effective sound transmitter, so it’s easy to make noise when colliding or moving it in the foundry. Foundry noise is another hazard vilolenting foundry safety.
Table of permissible noise levels for industrial factories nearby residential areas:
Acceptable | Complaints expected | Unacceptable | |
Day (7am-7pm) | 50-55 | 55-60 | 60+ |
Evening (7pm-11pm) | 45-50 | 50-55 | 55+ |
Night (11pm-7am) | 40-45 | 45-50 | 50+ |
The PEL is determined by the US Department of Labor depending on the number of hours exposed to noise. PEL increases gradually as the time to noise exposure decreases.
Table of PEL with hours of noise exposure:
PEL | Working time |
90 dBA | 8 hours |
92 dBA | 6 hours |
95 dBA | 4 hours |
100 dBA | 2 hours |
105 dBA | 1 hour |
110 dBA | ½ hour |
115 dBA | ¼ hour |
Noise exposed by foundry worker at the workplace should not exceed the exposure limits. If this noise limit is exceeded, your foundry workshop could be fined by the authorities.
What causes noise in the foundry?
There are many factors that cause noise in a foundry, the following are the main ones:
- Fettling and shakeout (90-115 dBA)
- Mechanical sand mixing and a forced draught furnace (90-100 dBA)
- Shot blast (100-110 dBA)
- Casting, sprue handling (95-115 dBA)
- Cast Grinding (92-115 dBA)
- Hammer-using area (95-100 dBA)
Noises | dBA |
Shakeout | 85-115 |
Inverter | 83-116 |
Air gauging | 82-107 |
Cast grinder | 95-115 |
Shot blasting | 85-110 |
Mold vibrators | 85-114 |
Hammers | 95-100 |
Mechanical sand mixing | 90-100 |
Casting, sprue handling | 95-115 |
The table shows the noise levels at different distances in a 1000 square meter foundry (assuming average noise levels are 85 dBA and 95 dBA):
Noise levels inside | 100m | 200m | 400m |
85 dBA | 52 dBA | 46 dBA | 40 dBA |
95 dBA | 62 dBA | 56 dBA | 50 dBA |
In addition to the workers directly involved in the above foundry work, others in the surrounding areas may also be exposed to noise levels of 85 dBA.
If exposed to noise levels of 85 dBA or more, foundry worker must join Hearing conservation program to test hearing.
How harmful noise exposure is?
- Effects on inner ear activities, hearing loss, tinnitus, and even deafness depending on the level of noise pollution.
- Causing difficulties in communication.
- Distracting with unrelated people.
- Affect the daily life of residents nearby the foundry, especially with noise in early morning hours or at night, affecting sleep and relaxation.
How to prevent noise in the foundry?
- Isolate the foundry worker from the source of noise by using sound enclosures.
- Regularly measure the noise level and the employee’s hearing to be able to control the noise without exceeding the noise exposure limit.
- Install sound deadening troughs such as aluminum liners, or external spray-on sound absorber.
- Improved working methods to reduce strong metal collisions that cause noise
- Use elastic surface coatings such as damping and deadening on the impacted structure causing noise.
- When buying new equipment or machinery, its noise level must be considered. Conduct a proper routine maintenance check.
- Install sound-absorbing materials for walls and roofs, to avoid foundry casting noise affecting citizens nearby.
4. Vibration hazard in foundry
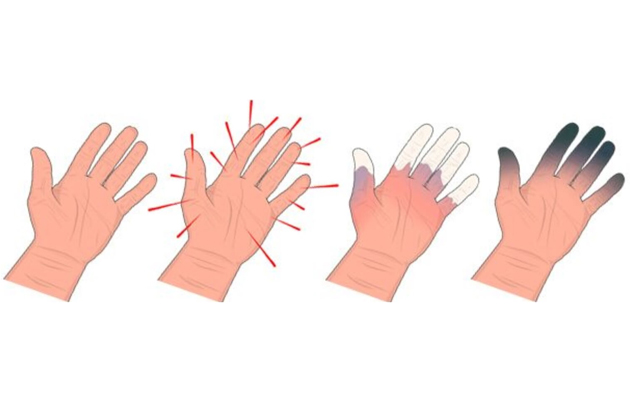
Vibration (usually whole body vibration) occurs frequently in foundries and has the posibility to compromise the health of affected people and volient foundry safety protocol.
Vibration and noise often come together because noise is caused by vibrations of the surface or atmosphere.
What causes vibration?
- Shakeout
- Sand slinging
- Forklifts
- Cranes
- Pneumatic ramming operations
- Hammers
Subjects impacted by vibration are those who directly operate equipment that vibrates or come into contact with a surface containing a vibrating device.
How harmful vibration is?
- Whole body vibration raises blood pressure, leading to heart problems.
- Neurological disorders.
- Stomach pain.
- Lower back pain.
How to prevent and minimize vibration?
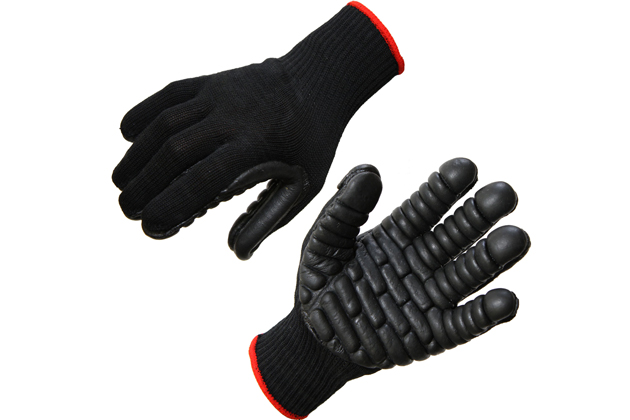
- Buy equipment with low vibration, and maintain them periodically.
- Process improvements to reduce the use of hand tools with vibration.
- Allow workers to rest alternately, avoid working in contact with continuous vibration.
- Wear padded gloves when using hand tools with vibration and full equipt with foundry ppe.
5. Heat stress in foundry
Working in a foundry often endures high heat loads from the working environment. Radiant heat is generated from heat sources that comes from molten metal transmitted in the air and metal surfaces that are dangerous to workers and violent the foundry safety.
Additonally, Arc columns also emit ultraviolet rays with great energy when melting metals.
What causes heat stress?
Heat radiation is emitted from the molten metal, primarily from metal melting in the furnace, by pouring the metal into the mold and by Convective heat transfer.
The temperature emitted from the kilns can be up to 400-500 degrees Celsius that are possible hazards at a foundry.
How harmful heat stress is?
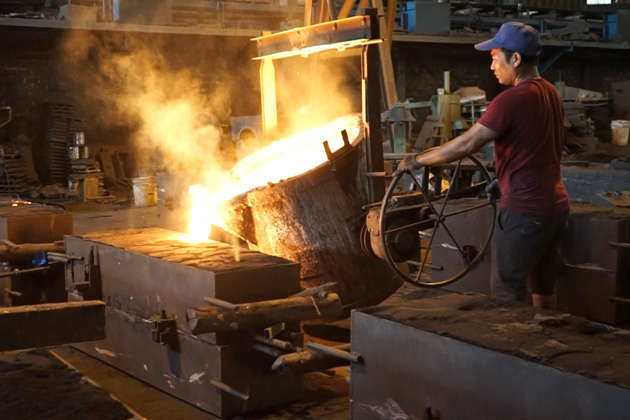
Heat stress includes heat stress inside the body and heat stress outside the body:
Heat stress occurs inside the body:
- Heat rash causes itching.
- Muscle cramps leads to pain.
- Heat stroke leads to exhaustion and nausea.
- Sweating can lead to dehydration.
- Stroke.
- Mental disorders, affecting behavior and perception.
Heat stress occurs outside the body:
Heat stress causes skin burns and blistering. It happens because foundry workers often expose to hot surfaces, heat radiation or molten metal splashes. With ultraviolet rays, when emitted infrared can also cause eye inflammation.
- Burn lever I, the skin will be red and painful.
- Burn lever II, the skin will blister and feel thick.
- Burn lever III, the skin will be white and hard.
The standard for casting temperature and personal contact accordingly to foundry safety protocol is 80 degrees C. If this limit is exceeded without worker safety equipment, burns will result.
To control heat stress, it requires:
- Install coolers, fans, air-conditioning, de-humidifiers to reduce humidity and cool the air.
- Install a ventilation system to make the air cool.
- There are rest rooms to avoid heat and adequate drinking water for workers.
- Measure the temperatures in the work areas as well as monitor workers’ heat stroke regularly.
- There is work rotation between workers to minimize time exposure to hot temperatures.
- Provide personal cooling or heat reflective clothing for workers who are frequently exposed to heat radiation.
6. Toxic chemicals in foundry
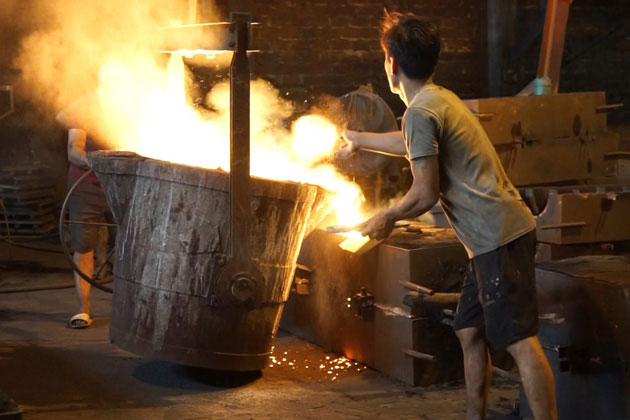
In the foundry work environment, the following chemicals are common used:
- Cleaning chemicals
- The adhesive used to make molds
- Catalysts
- Alloy components
- Gas in cylinders
- Surface polishing material
The following chemicals are produced during the casting process:
- Metal fumes from metal melting work.
- CO, SO2 are born during charging and melting step.
Please refer to the SDS chemical safety data sheet for the chemicals used and generated in the foundry for hazards and their response measures.
The chemical incident prevention and response measures in the foundry are similar to those given in the metal fumes and toxic vapor section.
7. Explosion in foundry
Explosions occur in foundries when water is poured into molten metal or molten metal is poured into damp containers, also known as molten metal explosion.
If equipments and tools are wet, encountering liquid metal at 1600 ⁰C, water will evaporate, volume increases suddenly, resulting in an explosion, and liquid metal splashes out that cause hazards at a foundry.
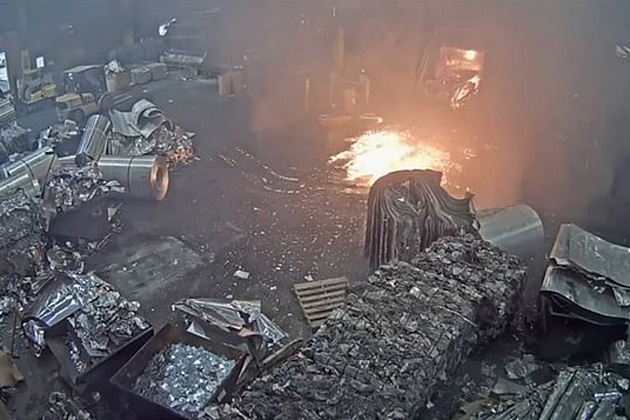
Cases of fire and explosion include:
- Liquid metal spilled out in contact with water.
- Charging furnace with wet ingots or crumbs.
- When wet tools, molds and materials are in contact with liquid metal.
Chemical explosions
Chemical explosions occur when chemicals come into contact with liquid metals, which can be oxidants such as ammonium, potassium nitrate, and oxidising salts that breach foundry safety protocol and cause hazards at a foundry.
How to prevent and minimize risks of explosion?
- Tools and materials used must be dried, not rusted and stored in a dry place.
- Equipment, tools and furnaces must be heated before being put into use.
- Do not allow water to enter the area with molten metal.
- Do not smoke or use fire in the area with molten metal.
- Classifying and storing chemicals, paints, solvents or combustible materials to avoid mistaking and catching fire.
8. Other injury in the foundry
In the casting area, in addition to the arrangement of machinery and equipment, in order to ensure foundry safety, the owner of the enterprise must also equip the labor safety system as well as foundry personal protective equipment (foundry PPE) for the workers.
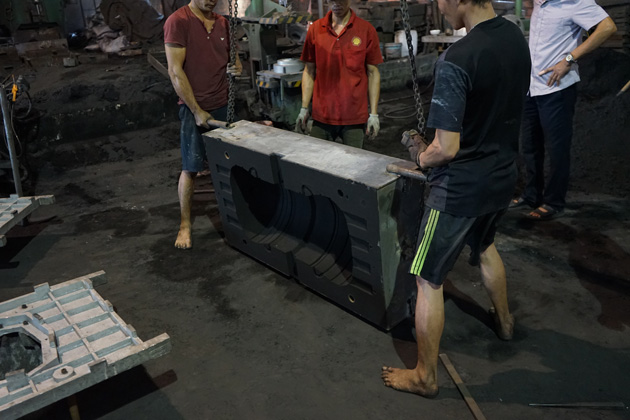
Causes of physical injury in the foundry
- Machinery and equipment contain dangerous factors (voltage, explosive mixture, vibration, …)
- The user of machinery and equipment is not proficient or does not comply with the regulations on labor safety.
- Lack of means of shielding, worker safety equipment from moving parts, dangerous areas such as high voltage, heat radiation, …
- The unreasonable layout of equipment and workplace, making operations difficult and easy to cause collisions.
- Do not clean, maintain, and clean machines and workplaces properly.
Common physical accidents:
- Collision: This usually occurs when cleaning the gating system and machining the casting leads to skin scratches due to contact with the sharp surface of the casting. Especially in the foundry, there are robotic arms or lifting devices, if not paying attention can lead to collisions.
- Flaking: During the melting metal or pouring metal into molds, liquid metals can be splashed, causing danger to the surrounding area.
- Slipping: In the foundry there are many metals and wires, if not arranged properly, it will easily cause tripping, slipping, or falling.
How to prevent and minimize risks of accidents in the foundry?
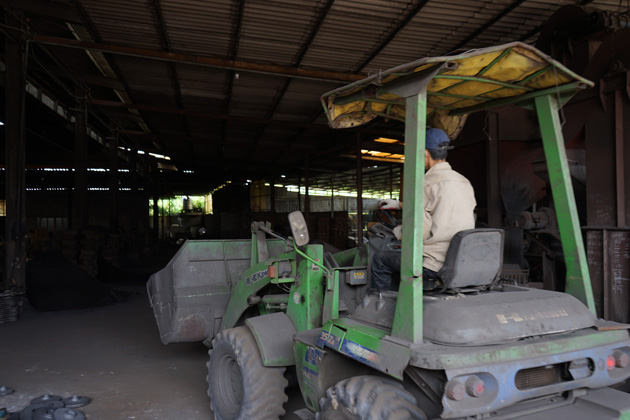
- The use of facilities, tools, and equipment in foundries must be done by specially trained persons to ensure the foundry safety.
- There are always foundry safety warnings and instructions and workers must comply with those regulations.
- The floor surface around the kiln must be made of anti-slip and fireproof materials.
- Install splash barriers in areas with molten metal.
- Equipped with emergency showers, hoses, safety blanket.
- Fully foundry personal protective equipment is required for workers working in hazardous areas.
- The foundation of the machine hammer must be located on the workshop floor and placed on the shock absorber base.
- The forging is fixed and fastened to the wooden base. The wood base must have a tight belt and buried 0.5m deep into the ground.
- When the furnace shell is red-heated, the oven must be stopped, let it cool naturally or cooled by compressed air, sweep the water and clay solution into the red heated place. During the operation of the oven, if the blower stops, the windpipes must be opened immediately. Only conduct oven repair when the temperature does not exceed 40 degrees C.
- With an electric furnace, only add ingredients or stirring metal when the power is turned off.
- The railing of the furnace must be 0.8m high, the door to pour raw material into the furnace must be 0.5-0.7m higher than the floor.
- The cast iron crusher must cover the height with ¾ of the maximum hammer lift.
- Do not pour metal into ladles or barrels exceeding 80% of their volume.
- Only carry metal by hand when the weight does not exceed 50kg. The aisle when transporting metal must be flat, at least 2m wide.
- Do not use compressed air to clean the casting but must clean in a closed chamber.
- The place of removing slag must be dry, have a shield to prevent slag from splashing.
Conclusion
Safety precaution in foundry workshop is very important because it not only ensures the safety of foundry worker but also ensures efficiency in casting.
In hazardous areas at the foundry, adequate steps should be taken to reduce unexpected accidents. Inspection, monitoring, assessment of hazards, and working procedures should be carried out or consulted by an appropriately qualified person.
Hopefully, through this article, VIC has helped you to have a detailed view of the hazards of working in a foundry, how to prevent risks, and ensure foundry safety practices.
If you want to use the article as a source of reference, please quote our website. Also, check our metal casting blog series to get more updates on metalworking techniques.
References:
https://www.safeworkaustralia.gov.au/
https://www.generalkinematics.com/blog/foundry-safety-part-1-noise-control/