Here we introduce 5 major types of sand casting defects commonly see in metalworking. You will find the cause behind each casting defect as well as remedies to prevent for improving casting quality.
Sand casting is the popular casting process in the metal foundry that creates the castings by forming the mold cavity in the sand container, pouring the molten metal, and breaking the sandbox to collect the casting.
This traditional and favorite casting method is advantageous because of its possibility of casting large volume, high detail, and low molding cost.
Like other casting processes (no casting is perfect even very innovative method), sand casting maintains imperfection.
Involved in a multi-complex process, sand casting arises a few concerns about the different type of defects that lower the product quality.
Metal casting defects are the imperfect conditions of the casting in comparison with the requirement that must be repaired, removed, or rejected. Some sand casting defects are small that can be acceptable tolerance, some can easily be repaired and machined. Some are severe that have no other way but reject and start another casting batch.
The key to prevent and minimize the metal casting defect as well as set the expectation and tolerance is knowing where irregularities come from and find the solutions to prevent them.
Grab these needs, here we list down 5 major groups of most popular sand casting defects seen in the metalworking and clear out the casting defect causes, and suggested remedies to enhance casting quality and deliver the best casting parts to your customers.
Casting shrinkage defects
The metal alloys shrink as they solidify in the mold cavity of the pouring step. It is a normal phenomenon in casting because the molten metal is less dense than the solid sort.
In the foundry, the shrinkage requires good calculation in the pattern and molding design.
Shrinkage defect is one of the most severe sand casting defects that lower the casting quality. Here casting shrinkage defects happen as the shrinking process occurs unevenly resulting in shrinkage cavities in the casting parts. Two types of shrinkage casting defects are close shrinkage defects and open shrinkage defects.
The open shrinkage defects can be detected in the casting surface by eyes, whereas, the close shrinkage (shrinkage porosity) defects are inside the casting.
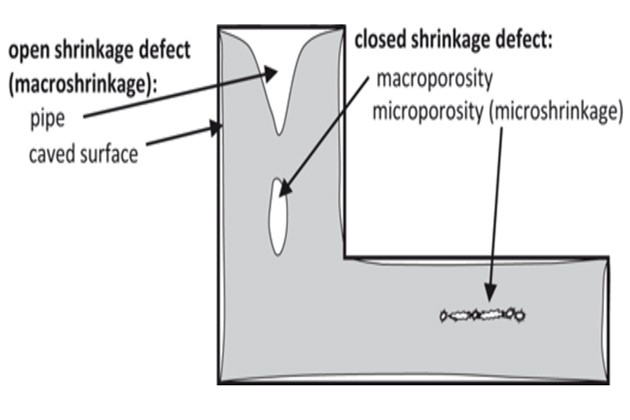
Open shrinkage defects
Open shrinkage defects are formed when the unevenly shrinking phenomenon occurs and draws the air inside the mold. They are split into two types: pipe and caved surface in the casting surface that can be observed by naked eyes.
Open shrinkage defects in sand casting lower the surface aesthetic causes crack, and weakens casting strength.
Close shrinkage defects
Close shrinkage defects, also known as shrinkage porosity, are cavities (holes) detected within the casting that is formed where a part of molten metal hotter than other material fluid. They come in micro-porosity or macro-porosity phase that can weaken the casting as well as worsening the corrosion-proof property.
Macro shrinkage porosity is a large cavity featured by rough and spongy surface, whereas, micro shrinkage porosity looks alike jagged marks or lines. Macro shrinkage porosity can be seen by naked eyes, while micro shrinkage defects are found by microscope.
What causes casting shrinkage defects in sand casting?
The shrinkage defects occur mainly due to the solidification of molten fluid is uneven or uncontrolled.
It stems mostly from improperly pouring structures and technical work as the following:
- Faulty gating and riser (feeder) system
- The pouring temperature is too high
- Mold wall shift due to high metal pressure
- Chills are not placed properly
- Sudden change in the thickness of sections
How to treat casting shrinkage defects?
The casting shrinkage phenomenon is an unavoidable, however we can reduce this metal casting defects by geometric and process modifications.
Below are factors you can intervene to enhance the final casting quality:
- Design a proper gating system to ensure the continuous flow of molten metal
The design of the gating system must ensure the criteria (1) Control the metal flow rate, not be impacted, not be swirled, not splashed, must be smooth and constant; (2) Fills the mold cavity quickly without losing metal dilution; (3) Controlling the temperature in the mold cavity to cool the metal stably.
- Design a proper feeder (also as known as a riser) system to compensate for the solidification contraction and minimize the shrinkage cavity formation
The riser is a molten metal storage cavity used to supply molten fluid to the mold cavity to compensate for shrinkage during metal solidification.
The two criteria to design a riser system include:
(1): must contain enough molten fluid volume to compensate for the solidification contraction.
(2): must place in the final solidification position of the casting, later solidification than the casting and is in the liquid state for the longest
The Riser volume is calculated by this formula:
Vf ≈ αVc
In which:
Vf is the riser volume
α is shrinkage fraction
Vc is cavity volume
- Limit the total volume deficit by reducing casting temperature
- Inserting internal chill, cooling ribs, or cooling coil to increase local heat dissipation
A chill, cooling ribs, or cooling coil, is used to enhance the solidification process in a casting section of the mold. It should be a place where heat tends to pool such as pick and heavy sections.
Gas porosity
Gas porosity is another popular sand casting defect mostly seen in the metal casting process. Gas porosity is bubbles created within the casting after the cooling step. Gas porosity casting problems come in three types of bubbles that are pinholes, blowholes, and open holes.
These casting problems occur because there is an amount of gas (nitrogen, oxygen, or hydrogen) contained in liquid metal but not in solid metal. Hence, when the fluid is cool down, this amount of dissolve gas forms bubbles that lower the strength, ductility, and aesthetic of the casting products.
These bubbles present as porosity or pore either on the surface or inside the casting. The pore can vary from 0.01 to 0.05mm for a few kg of casting, whereas, the pore of larger weight casting can be 0.04mm in diameter.
Pinholes
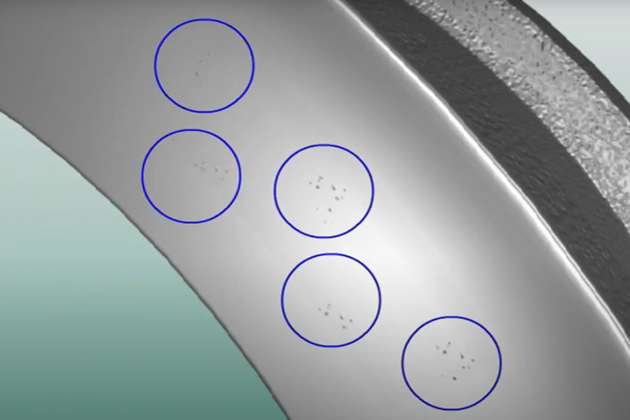
Pinholes, also called as porosities, are tiny bubbles mostly gathered in the upper surface of casting parts. It usually sizes about 2mm and can be detected by naked eyes without professional inspection equipment.
Blow hole
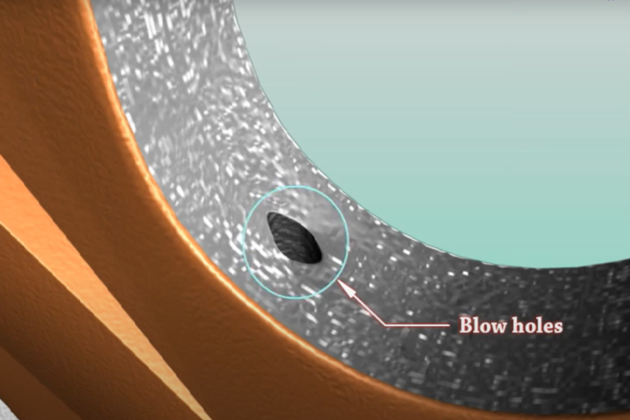
Blowholes, as known as blows, are larger cavities than pinholes that usually appear inside the casting parts. It is invisible to the naked eyes.
To detect the interior casting quality, x-ray, harmonic, ultrasonic, or magnetic analysis are applied to scan blowholes. Blowholes also can be found in the machining steps.
Open hole
The open hole is similar to large cavities as blowholes but it appears on the surface of casting parts that visible to naked eyes.
What causes gas porosity in sand casting?
Gas over-absorption mostly occurs by too much moisture and badly vent set up. Specifically, reasons can be listed as follows:
- Too much high moisture in sand molding mixture
- Molten metal transport tools (ladles) are wet
- Gasified sand is insufficient
- Over high temperature of molten metal
- Chills contain rust and moisture
- The core is not enough baked
- There are insufficient vents in a sand mold
- The sand mold is over rammed
- Metal turbulence during pouring step
How to treat gas porosity defects?
Proper practices of casting foundry can minimize the gas porosity and ensure the casting quality. By these following works, it can reduce gas trapped in the metal and avoid cavity formations:
- Control the adequate moisture content in the sand mold and ensure molding sand is dry and permeable
Notice that the sand which is too fine can weaken the sand mold gas permeability. It is recommendable to use coarser sand for better gas permeability.
Also, do not excessively rammed the sand mold because it can lower sand mold permeability too. Create more vents in the sand mold by vent rods for better permeable. Additionally, the mold requires to be dried in a standard drying manner.
- Molds and core are required to be dried and stored in a standard drying condition
- Ensure to design enough vents for sand mold and cores to allow gases to get out.
- Use un-rust, clean chills, and dry tools
- Apply properly melting and pouring processes
To minimize the gas porosity casting problems, it is highly recommended to melt metal material in a vacuum surrounding by a low-solubility gases environment or under the flux that prevents air contact with the molten metal. Also, pouring molten fluid at a lower temperature to increase the solidification rate and reduce gas absorption.
Moreover, the turbulence in metal pouring can introduce gases hence it requires a proper gating system design to prevent metal turbulence during pouring.
Pouring metal defects
Pouring metal defects are formed by the improper molten pouring process into the mold cavity.
This casting problems category into four types that are cold shut, misruns, and slag inclusion.
Cold shut in casting
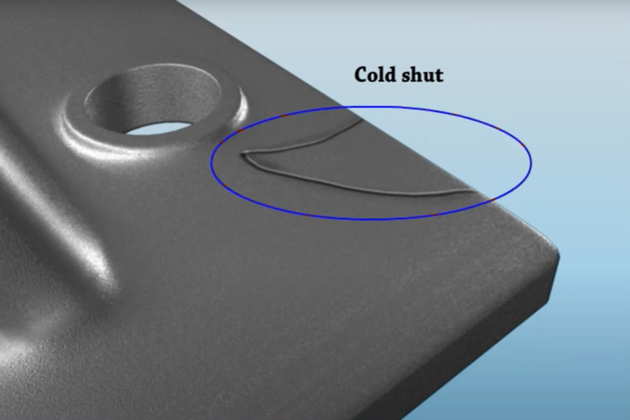
Cold shuts in casting are lines or cracks formed in the middle part of the casting surface in a rough edge resulting in a weak spot. Cold shuts are visible by naked eyes and castings are often rejected if containing cold shuts defects.
These sand casting defects weaken the strength of the casting that is able to break the casting.
These sand casting defects occur as the molten metal is poured into the mold cavity from two pouring points, but the two flows of molten fluid don’t fuse properly.
What causes cold shut defects?
The cold shut defects come from:
- The molten metal is lack of fluidity
- The gating system is designed improperly
How to treat cold shut defects?
The main reason causes cold shut casting defect is the lack of molten metal fluidity. Here are solutions to enhance the fluidity of the metal liquid:
- Design the gating system properly
- Limit premature solidified process by increasing the pouring temperature
- Use coarser sand to enhance the sand mold permeability
Misruns
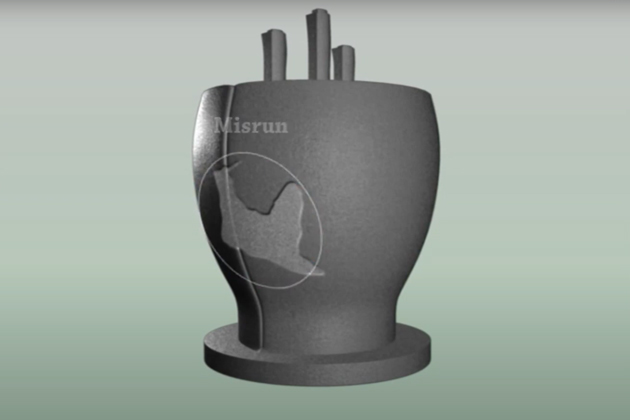
Misruns are casting defects in which the mold cavity is not filled completely with molten metal resulting unfilled portions or missing parts.
This happens because the metal fluid becomes freezing before filling the entire mold cavity.
What causes misruns defects?
The reason leads to misruns casting defects are similar to cold shut that is lack of molten metal fluidity.
How to treat misruns defects?
Similar to cold shut remedies, if your casting faces misruns phenomenon, do check
- Gating design
- Sand molding design
- Pouring temperature
Slag Inclusion
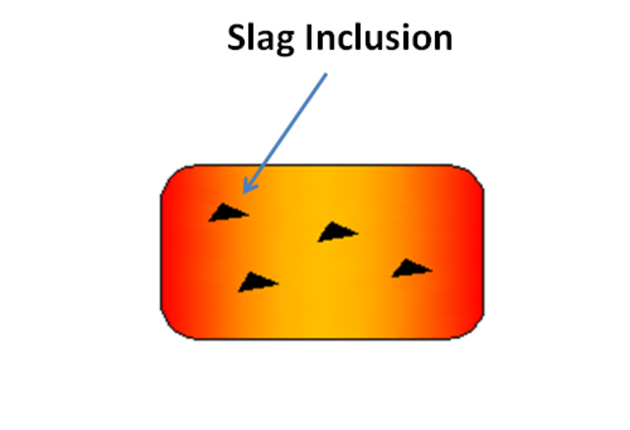
Slag inclusion is dark gray clusters or single distribution found in either surface or inside the casting.
It is usually detected in the sandblasting and machining processes.
What causes slag inclusion?
The reasons that slag inclusion defects are formed including:
- The raw material and melting input contain impurities (oxides, nitrides, carbides, sulfides, etc.)
- The improper pouring system design leads to slags are drawn into the mold cavity during the pouring process
- Material that is eroded from melting furnace, pouring cup.
- Contaminates that contain sand mold
- Slag is not removed and cleaned after the refining step, plus alloy liquid is excessively stirred under high temperature causing reoxidation
How to treat slag inclusion?
There are several ways to minimize the concentration of slag inclusion. To prevent the slag inclusion from forming in the casting, you can check these remedies:
- Control the raw material and melting input
It is suggested to put raw material into SpetroMax composition analyze machine to check the input material quality. Also, clean and remove impurities from the melting material and store them properly.
- Qualify the metal melting process to ensure the pure alloy liquid obtained
To prevent oxide formation in the metal, it is recommended to melt metal in a vacuum, flux, inert atmosphere.
If you melt metal in a normal furnace, make sure it is well control of input material, additives, and melting temperature. Remove all the slag formation in the furnace during melting.
- Optimize the pouring system
Set up filter layer, skimming, slag collection parts in the pouring system design to minimize the slag inclusion into the mold cavity.
- Properly pouring technique
Use pouring cup with slag blocking section. Pour slowly, continuously, and evenly to make sure the liquid flow doesn’t break. Remember not to use the small volume ladle (pouring cup) to fill the larger mold cavity.
Mold material defects
The sand casting process uses naturally bonding sand mold that arises casting defects relating to the mold. Mold material defects are problems resulting from molding material and mold design.
There a different mold material defects, here we list down the main defects commonly seen in the casting process.
Cuts and washes
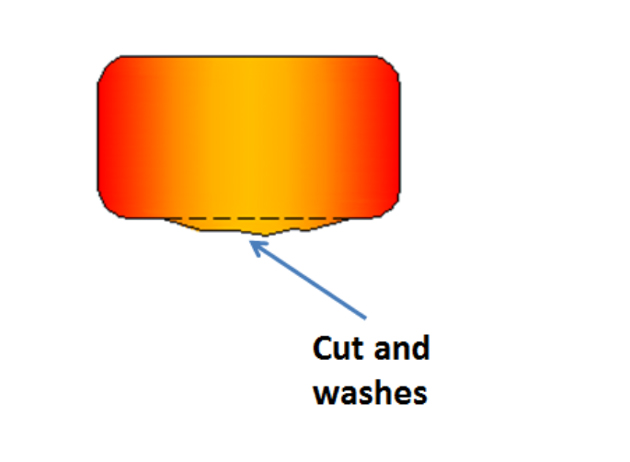
Cuts and washes are common sand casting defects that created because the molten metal erodes sand mold causing excessive metal casting parts. Cuts and washes defects present as low bulges located along the casting surface and tilted to the end that has more pouring pressure.
What causes cuts and washes defects?
The cuts and washes defects occur due to:
- Too much high velocity of molten metal in the pouring process
- Improperly gating system design
- Low strength of sand mold and core
- Lack of binder in the facing and core stand
How to prevent cuts and washes defects?
To prevent cuts and washes defects, you can try to adjust these things:
- Design a proper gating system
- Enhance the strength of sand mold and core by adjusting sand molding mixture (sand grain size, clay, moisture content) and controlling molding technique
- Add binders in the facing and core stand
Metal penetration
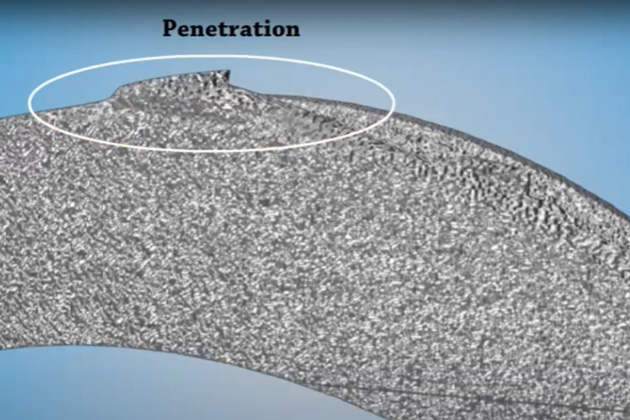
Metal penetration is the casting defects that metal penetrates sand grain gaps resulting in a rough and uneven casting surface. These sand casting defects are visible to naked eyes and lower casting aesthetic.
What causes metal penetration defects?
Metal penetration phenomenon occurs due to:
- Use too much coarse sand grain
Too much coarser sand grain (large grain size) is more likely to cause metal penetration severely than fine sand.
- The sand mold is rammed too soft
- Sand mold and core are low strength
- No mold wash
How to prevent metal penetration defects?
To prevent these sand casting defects, solving the above causes by:
- Use the small sand size
- Increase sand mold and core strength
- Provide enough hard ramming to the sand mold
- Apply a mold wash to add a protective layer against metal penetration
Fusion
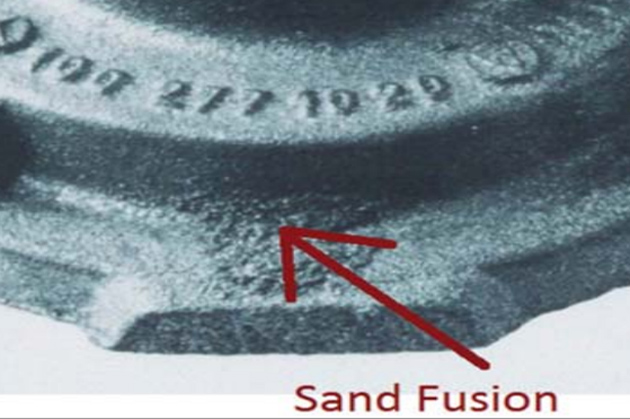
Fusion is sand casting defects in which sand grain fuses with metal flow resulting in a thin crust with a glassy and brittle look attached to the casting.
What causes fusion defects?
Fusion defects occur mostly due to:
- The sand mold has low refractoriness property
Refractoriness is the molding ability to withstand the molten metal temperature to be poured helping prevent the metal fused possibility.
- High pouring temperature
- Improper gating system design
How to prevent fusion defects?
Prevent fusion sand casting defects by:
- Design proper gating system
- Lower the pouring temperature
- Higher the refractoriness property of sand mold by adding silica sand
Runout
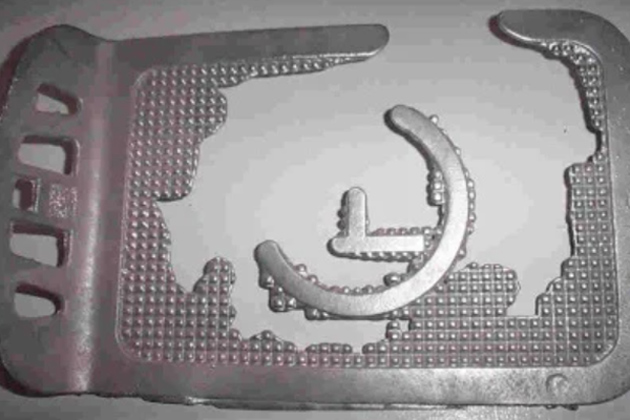
Runout is sand casting defects that molten metal escape out of the mold resulting mold cavity is not entirely filled and missing/incomplete parts are created.
What causes Runout defects?
Runout defects come from 2 main reasons:
- Low precise mold design
- Improper flask (a toolbox to contain sand mold)
How to prevent Runout defects?
Solutions to prevent runout defects are:
- Design a precise sand mold. Rejects unqualified sand molds before pouring step
- Choose high-temperature resistance material for sand mold to prevent wear and tear
Swells
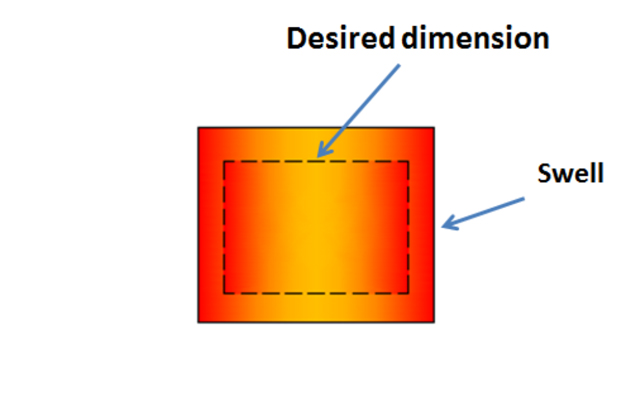
Swells cause enlargement of casting compared to the desired volume that requires further machining later and metal wastage.
What causes swells defects?
Swells casting defects reason from:
- Low strength of the sand mold
- The sand mold is badly rammed
How to prevent swells defects?
Prevent swells casting defects by:
- Hard rammed sand mold
- Increase the strength of sand mold to bear the molten flow pressure
Metallurgical defects
Metallurgical defects come as there are problems in casting metal. Two casting metallurgical defects are hot tears and hot spots.
Hot tears/cracks
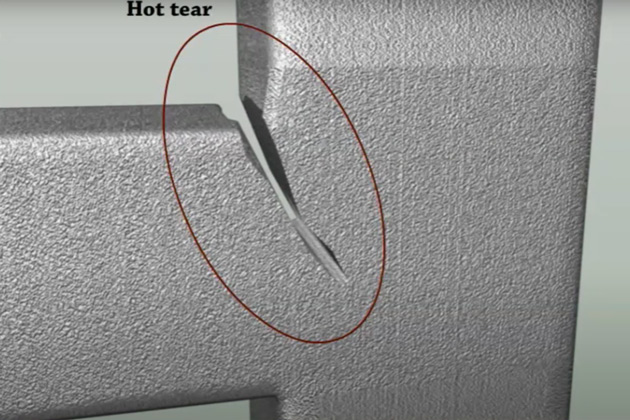
Hot tears, as known as hot crack, are sand casting defects that appears as irregular crevices in the casting. Some cracks are visible to naked eyes, some need magnification to detect.
These cracks are created because the metal is weak when it is hot, and residual stresses (tensile) in the metal can cause problems as it solidifies. If solidified metal doesn’t have enough strength to resist the residual stresses, the hot cracks will present.
What causes hot tears defects?
- Improper mold design
- The sand mold is lack of collapsibility
- The sand mold is too hard rammed
How to prevent hot tears defects?
- Proper mold design to enhance the collapsibility
- Soft rammed sand mold
Hot spots/Hard spots
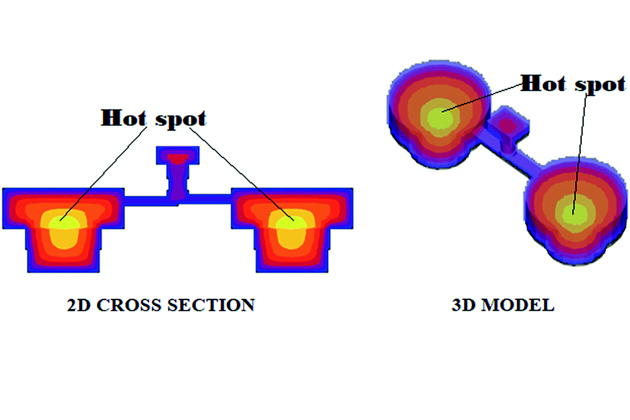
Hot spots, also called hard spots, happen when a casting area is cool quicker than other surrounding areas resulting in hard spots than others.
What causes hot spots defects?
- Improper cooling practice
How to prevent hot spots defects?
- Provide proper cooling practice
- Adjust the metal composition
How does our foundry treat sand casting defects?
As mentioned at the beginning, no casting process is 100% perfect. Although featuring excellent casting properties, there are casting defects to be concerned about.
Specifically to one of the most favorite and popular in casting foundry that is sand casting. It can not negate that sand casting is exceptional by its ability to cast large volume, high detailed and low molding cost of casting parts. However, it is vital to look at possible sand casting defects to estimate the tolerance and expectation to customer.
At VIC casting foundry, we are transparently to discuss with our customers possible casting defects that could happen during the working process. We always try to limit as much as possible to minimize sand casting defects and supply the best quality casting parts.
Our approach to sand casting defects varies from different defects. However, our working motto is always prevention is better than cure. Therefore, we apply strictly inspection processes for all of the manufacturing processes, from raw material input, melting metal, pouring system, cooling, to machining work.
At VIC foundry, we have equipped with SpetroMax machines to analyze input material composition. Before every melting segment, the raw material is well controlled of its quality to reduce the metallurgical defects. In this way, we can limit the casting defects in the first place.
At the same time, we continuously control the gating system and pouring process to ensure its effectiveness and properness in accordance with each casting requirement. All the mechanical processes are under the supervision manager to ensure proper technique.
After the casting cools, all of the roughcasting must go through the filtering process to sort out qualified and unqualified objects. Any under-required casting continuously is moved to machining steps. The casting will be rejected if they are impossible to repair.
By this way, we can guarantee to commit that whatever casting we offer to the customer, it is of high quality.
Read more:
How are kettlebells made by sand casting?
—–
Reference
Sadaf Vazehrad (2011). Shrinkage Porosity Characterization in
Compacted Cast Iron Components. https://cdn.intechopen.com/pdfs/73849.pdf
Nawaz Mahomed. Shrinkage Porosity in Steel Sand
Castings: Formation, Classification
and Inspection. http://www.diva-portal.org/smash/get/diva2:643746/FULLTEXT01.pdf
Good information