Sand casting is a metalworking process in foundry that uses sand as the molding material, allowing for low-cost casting of unique metal shapes. Sand casting molds are the indispensable parts in the sand casting process and play the vital role in casting a range of industry applications. In this blog, VIC will help you get more knowledge about how to make sand molds for metal casting in a simple and easy way to understand.
What are sand casting molds in the metal casting?
Sand casting molds are molds used in metal casting that used once after pouring metal fluid and being broke to collect the casting. The collected casting shaped in a sand mold features low precision, poor surface finish, and a large metal excess that would require post-machining.
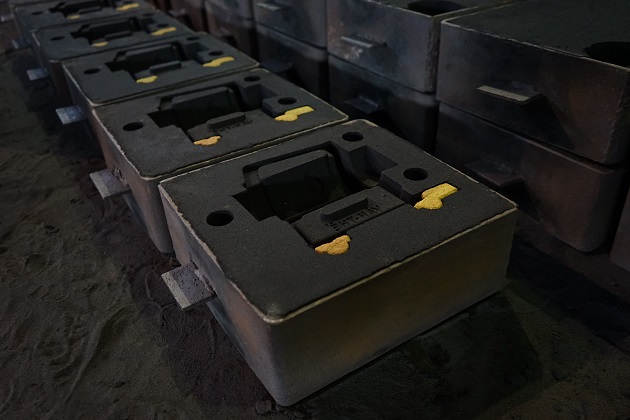
Sand molds are advantageous on making intricate and heavy mass casting plus low molding cost.
To make sand casting molds for metal casting, whether at the foundry or at home, the molding process must be done in a well-ventilated area to avoid dust from sand and smoke from molten metal.
Explain How to make molds for metal casting in video:
Things to prepare before making molds
Prepare technical issues
- The technical department bases on detailed drawings to create drawings of casting, pattern, cores and allowances to make patterns more accurate.
- Create patterns, cores, and gating systems from the drawing. Pattern gives the outward appearance while the core gives the inner shape of the casting. The gating system is to guide molten metal and release air for the mold.
- Determine components in the molding mixture to ensure the properties of the mold.
What are sand casting mold’s properties?
- Refractoriness: is the ability to prevent the mold from flowing into the casting when pouring liquid metal into the mold.
- Permeability: During casting process, a large amount of the generated gas needs to be released out of the mold. If not so, the casting defects can be created.
- Strength: When a mold is subjected to external forces such as moving, assembling, or molten metal pouring, it must retain both inside and outside shape.
- Collapsibility: sand casting molds must be elastic so that when the object is condensed, it will not be obstructed by the mold leading to warping and cracking.
- Cohesiveness: Helps sand to retain its original shape after removing the pattern from the mold.
Sand casting molds mixture
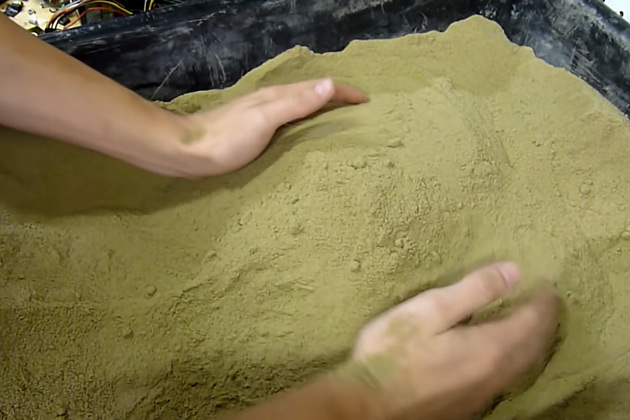
The sand casting molds mixture includes:
- Sand: is divided into sand coat and base sand.
- Bentonite clay is mixed with sand to help create durability for the mold. Bentonite also absorbs more water which increases its binding strength.
- Binders (often using vegetable oils, water-soluble substances) help increase the strength and flexibility of the mold mixture.
- Auxiliary substances (sawdust, coal powder, straw) help increase the air permeability for the mold and at the same time help the sand mold mixture resist heat better.
The above substances are mixed in certain proportions depending on the casting.
Currently, green sand mold mixture is very popular in sand casting technology because green sand has natural moisture that increases the strength of the mold.
Prepare equipment to make sand casting molds
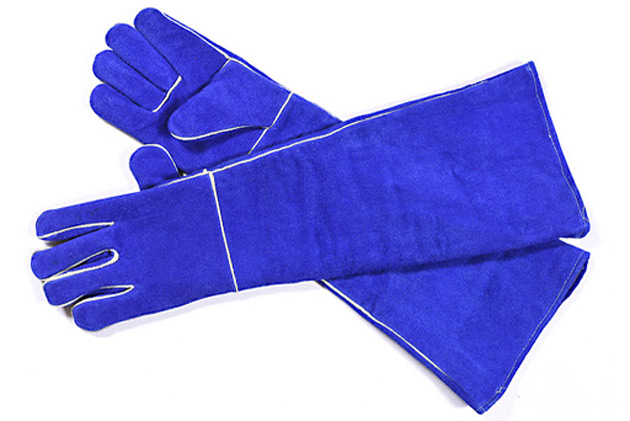
- Pattern: Read pattern making article.
- Powder or chalk dust: Powder is coat on the surface of a pattern to prevent sand from being sticking on. It is also covered the surfaces of the cope flask and drag the flask so they do not stick together.
- Sand coat: used to coat the pattern to give it high flexibility. Sand coat in direct contact with liquid metal and accounts for about 10-15% of sand for molding.
- Base sand: used to make molds or cores. Base sand must have high air permeability, accounting for 60 – 90% of the total amount of sand in the mold.
Currently, sillica sand is the most popular sand for base sand since it is readily available and cheaper than other types. In addition, it has all the properties needed to make molds as outlined above.
- Cope flask and Drag flask: are two upper and lower halves of the mold, separated by parting line (also called parting plane). You can buy flasks on internet or make it from wood.
- Mold Jacket: is a metal box that fits in the sand casting mold to support the structure of the mold and ensure that the mold does not break when being moved.
- Sprue: is a funnel that leads liquid metal from a pouring cup into the tapered sprue, then through the runner, going into the gates one after another.
- Sand compactor: used to compact the sand in flask to make the casting surface more detailed and reduce the time to clean the casting. You can use a pestle or shovel to compact the sand as alternative choices.
- Sand sifter: filter sand to be finer and cleaner.
Prepare protective safety equipment for sand casting molds process
- Safety glasses: protect your eyes from debris and dust.
- Gloves: keep your hands safe from dangers in the foundry such as cuts, burns, abrasions…
- Safety boots: The shoe’s toe is armored to protect the toe tips from falling, collisions or being attacked by heavy objects.
- Long pants: they are protective pants with thick fabric to protect your feet from heat, impact…
How to make sand casting molds for metal casting?
1. Making drag molds
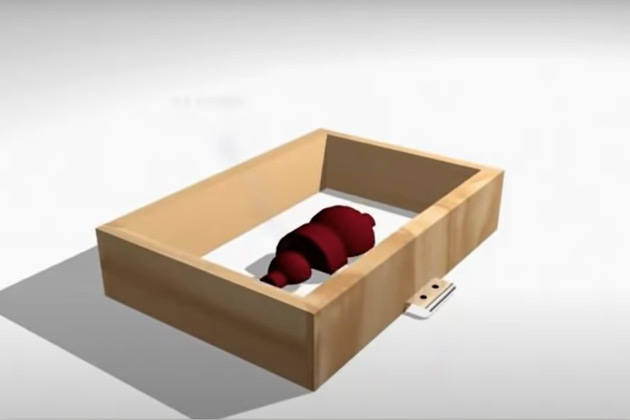
- Place the pattern on the pattern plate. Parting planes are in contact with pattern plate.
- Put half a cup of chalk dust into a sock or a small cloth bag. Sprinkle evenly on the pattern surface to help the sand not stick to the pattern when pattern removal.
- Fill the sand base into the mold through sand sifter. Remove sand lump through sifter.
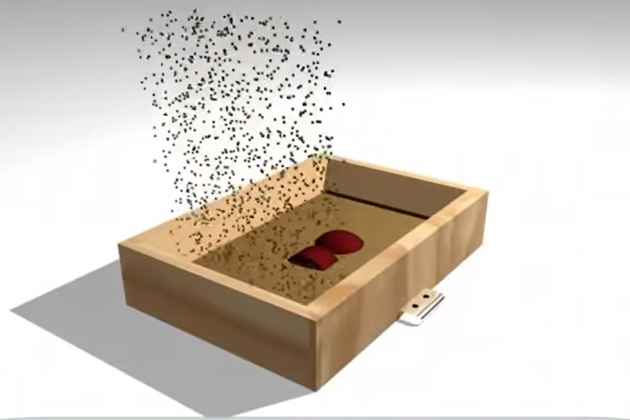
- Use a pestle or shovel to compact the sand in the mold so that it is tight and evenly from the edges to the middle. This step creates the mechanical strength of the sand mold to help the mold cavity shape be more detailed. Make sure all corners are tight.
- Flatten the upper surface to clean the excess sand.
- Oblique holes 40mm apart to allow air to escape.
- Flip mold 180 degrees.
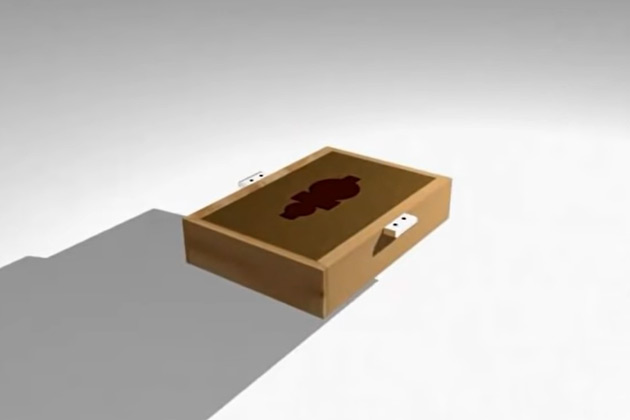
2. Making cope mold
- Place the other half of the pattern on top to exactly match the pattern in the drag flask.
- Attach the upper mold to the lower mold to match the connecting rod.
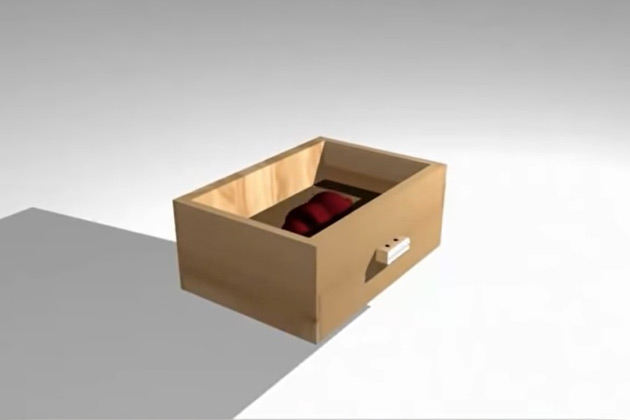
- Arranging pouring pipe by using sprue to create holes to lead into mold cavity. This is where the liquid metal will be poured into the mold during the casting process.
- Fill sand in and remove excess sand like with drag flask.
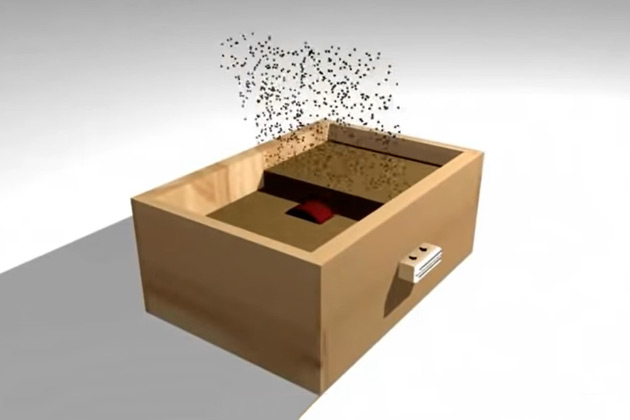
- Cut the pouring funnel.
3. Remove pattern
Make sure the drag flask is located under the cope flask.
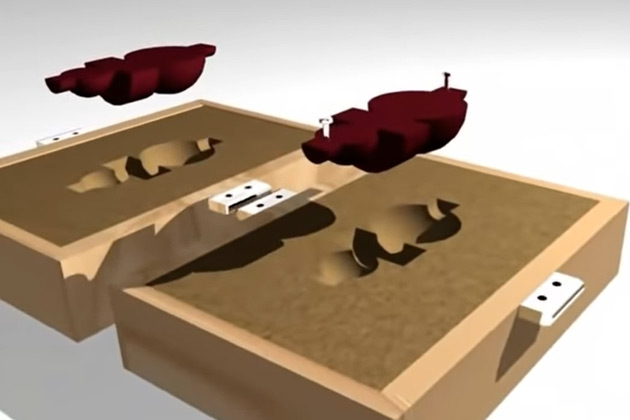
- Pick up the cope flask set aside and rotate 180 degrees. You can now see the pattern placed in the flasks.
- Cut the dirt trap through the pouring pipe.
- Smooth the part of the mold in contact with the pattern.
- Slowly remove the pattern from the drag flask and cope flask in the vertical direction.
4. Assemble molds
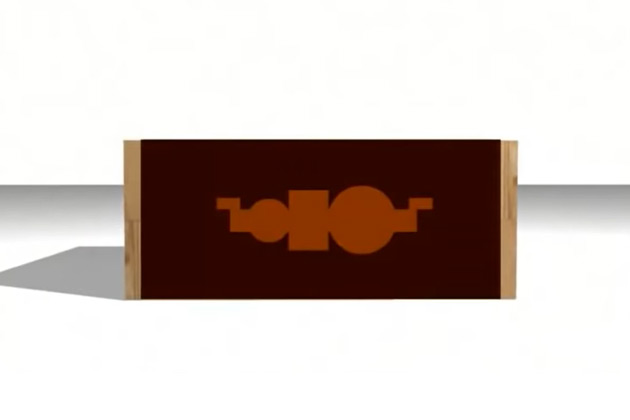
In case the casting has holes, the core must be inserted in the correct position in the mold (see core & core print). The core must be painted and dried and polished.
- Place the cope flask on top of the drag flask, they must be aligned in the same fashion as they were with the pattern.
- Attach the respective flasks fixed together. Then remove both flasks slowly upwards carefully to avoid damaging the sand casting molds.
- Set mold jacket over the sand mold to increase the stability of the mold. Do not tighten much to avoid deforming sand molds.
Thus, set of sand casting molds are finished. You just need to pour liquid metal into the pouring funnel, then wait for it to cool down and break the mold to collect the roughcasting in accordance with the designed pattern.
With the VIC casting method outlined above, whether you are a DIY casting or casting business, you can still fabricate a set of sand mold for your foundry.
VIC is a skilled foundry using a variety of casting technologies. Sand casting is one of the key casting technologies of VIC. To build a business partnership with VIC, please contact us here.
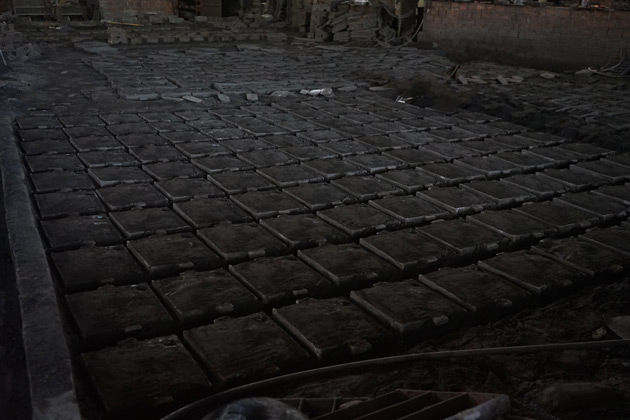
Remember to follow VIC’s articles on casting, if you want to use our articles as a reference, don’t forget to credit the source.
Read more our article:
How are kettlebell made by sand casting?