Lost foam casting is often used to cast small to medium complex products from some metal alloy materials. The final products maintain high precision and good surface finish.
Continue series blog of casting technology of Vietnam Cast Iron, this article will bring a brief and concise summary about the lost foam technology which often used to cast high detailed products.
The author will provide a detailed explanation including definition, advantage & disadvantage, and application of the lost foam process so that everyone could be easy to have a clear idea about this metal casting technology either you are an expert or freshman to this mechanical industry.
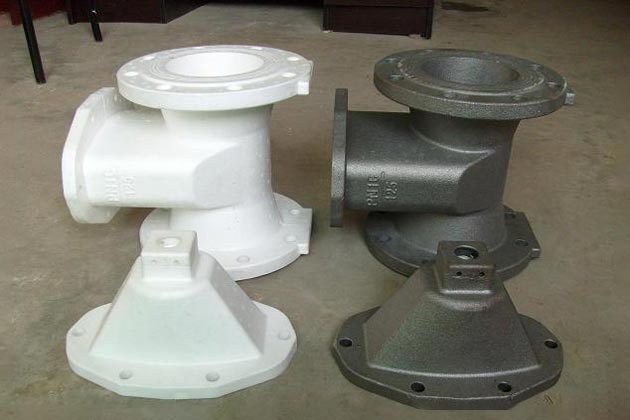
What is Lost Foam Casting?
Lost foam casting is a type of evaporative pattern casting. This method is quite similar to investment casting which uses wax instead of foam in the pattern making process.
The foam pattern was first used in metalworking in 1958. Although this mold casting technique is not as popular as other methods such as sand mold casting or permanent casting, it maintains outstanding advantages, especially in casting complicated and precise molds.
Unlike traditional methods which include the pattern withdrawn process before casting and require skillfulness in the pattern removal step, with respect to the lost foam method, the pattern is evaporated when the molten metal is poured into helping to reduce these considerations.
The lost foam casting process
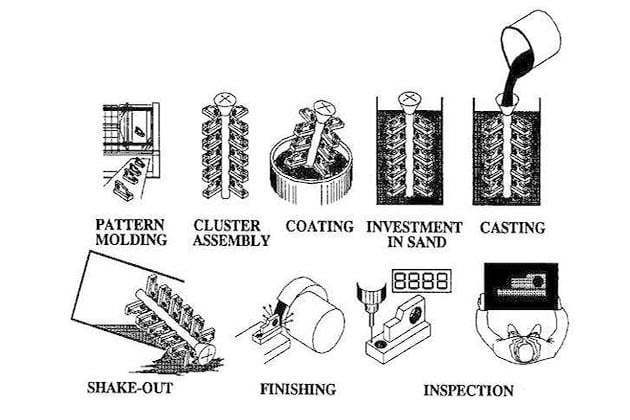
The lost foam casting technology included 5 steps: designing the pattern; applying insulation painting; placing the pattern into the sand flask; pouring the molten metal; and collecting the castings.
How a lost foam pattern is made?
Firstly, a pattern is designed from polystyrene foam. This type of foam plays an important role in this casting method. It is a good thermal insulator and chemical resistance, enable working normally at the temperature below 75 oC.
Depending on difficulty and details of the product, the foam pattern can be made from different manners.
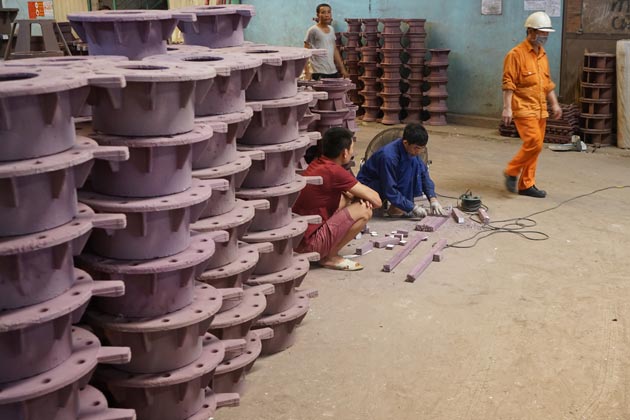
For highly detailed casting patterns, the foam pattern is partly made and glued together. For the small volume, foundries often make patterns by hand-cut or machined from a solid foam block. If the pattern is simple enough, a hot wire foam cutter can be applied.
In case the volume is large, the pattern can be mass-produced by a process similar to injection molding.
Polystyrene beads are injected in a pre-heated aluminum mold at low pressure. After that steam is applied leading to polystyrene expands more to fill the empty cavity and then form the pattern or a section. The final pattern is approximately 97.5% air and 2.5% polystyrene.
Casting process
Once the pattern is formed, it is coated with insulation paint, placed in a flask and surrounded in un-bonded sand and compacted.
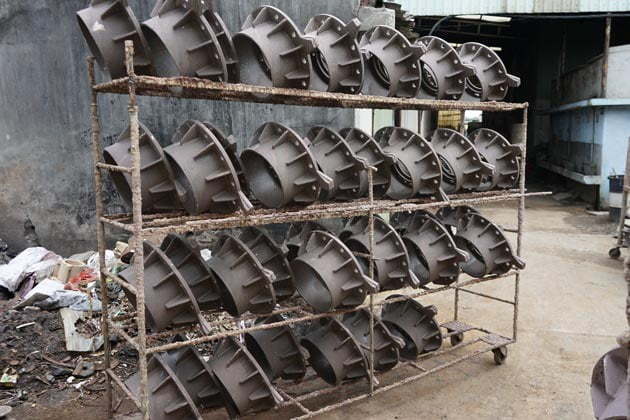
The covering paint works to increase the durability of the mold surface, protect from erosion, and broken. Whereas, the flask is designed suitably for this method so that when the molten metal is poured into the mold, the gas generated by foam burning is withdrawn completely.
After molten metal is poured into the foam pattern, the foam pattern is burned out and the casting is formed.
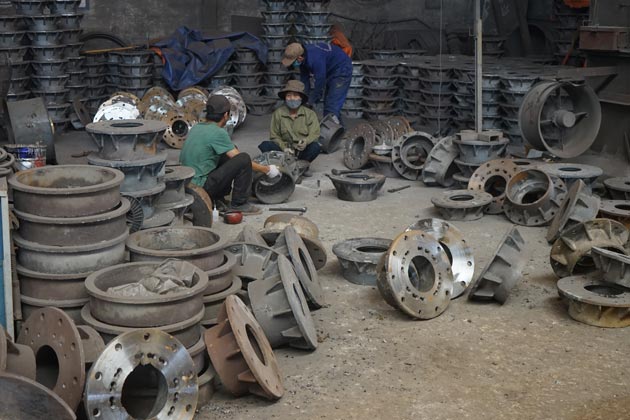
What are the advantages of the lost foam casting process?
Lost foam casting maintains excellent advantages in comparison with other metal casting methods.
- It is able to cast very complicated castings.
- It is advantageous for guaranteeing high precision and smooth surface finish.
- Casting by the lost foam technique guarantees nearly no errors or defects.
- Generally, this method is also more economic than investment casting because it involves a few steps. Applying the lost foam process, the foundries can save a lot of labor and production costs.
What could be disadvantages of the lost foam casting process?
Except from numerous advantages, there are two main limitations of the lost foam casting technology.
- Firstly, the pattern costs can be high for low volume applications.
- Another disadvantage is the patterns are damaged or distorted easily because of its low strength.
Application of Lost Foam Casting
Lost foam technique can apply in various materials ranging from alloy steel, carbon steel, alloy cast iron, ferrous alloy to alloy aluminum.
Ignore a few limitations, there are various advantages found in the lost foam method. Because of its precise casting ability, this process is often preferable to cast complicated and detailed products.
It is applied in a variety of industries ranging from the arts, computer technology, agriculture, national defense, automotive, to civil areas.
For many cast products cylinder heads, cylinder blocks, pipe fittings, valves, fire hydrants, motor starters, 3D models, gearbox details and more the lost foam casting process is the perfect match.
High detailed and complex lamp posts, gas burners, fences, pump housing, aluminum castings, pan support, etc. are also often processed by the lost foam casting.
Lost foam casting in Vietnam
-
Lost foam workshop -
Foam pattern in lost foam casting
Together with sand casting, the lost foam technology is most widely and popular applied in metalworking foundries in Vietnam because of its economic effectiveness and good quality.
Vietnam Cast Iron is the leading company in metalworking. We supply custom-designed products meeting international standards within fields as following:
- Urban Decoration
- Agriculture Machinery
- Construction Industry
- Transportation
- Marine
- Water Supply and Drainage
Our productions are mainly made from cast iron, ductile iron, carbon steel, and aluminum; and processed by three main innovative technologies including Green Sand, Lost Foam, and Furan Sand.
With respect to the lost foam technique, we often recommend this method for high-detailed products. The outcome delivers tight tolerances, good surface finish, and save cost for the buyers.
Lost foam technology is an efficient and economic process. At Vietnam Cast Iron, with numbers of high skillful and expert labors and high-tech machinery, we could manufacture almost any products by the lost foam process, from a lamppost, manhole cover, pump housing to trash bin, fence, gas burner, etc.
We work with our customers to decide the best casting processes resulting best quality for final products and minimizing the buying cost.
Request a quote to get more information on how our casting service can match your project requirements.
Contact information
- Company: Vietnam Cast Iron Co.Ltd
- Address: Lai Xuan, Thuy Nguyen District, Hai Phong city, Vietnam
- Email: [email protected]
If some one wants expert view on the topic of blogging after that i advise him/her to visit this weblog, Keep up the nice job.|