Melting metal is the process that transforms metal from solid sort to liquid sort. The melting process varies in technologies. Here we provide an explanation of how to melt metal in a foundry plus common metal melting points and protective safety protocol.
The casting foundry mainly deals with working on molten metal to shape a variety of casting applications. It is not exaggerative to appreciate that melting metal is the heart of the foundry.
Melting metal is an indispensable casting process that liquefies the solid metal to pour into the mold and form the casting in whatever shapes. Briefly, on its working process, the metal is put into a melting device called a furnace and overheat up to a certain melting point to transform the solid metal material into a liquid sort.
There are different technologies applied in melting metal, mostly depends on the type of melting furnace is used. In this post, we help you answer the concern “How to melt metal” by specifying the main melting furnace technologies in foundries today, plus the melting point of common metals as well as guidance on safeness protection in the melting process.
Stay with us and dig out the knowledge!
What is the melting metal?
Melting, also called fusion, is a transition process that changes metal material status from solid sort to liquid sort by providing enough heat.
The melting metal process loosens the tight packing of metal molecules. As the result, the melting gives metal liquid out of the solid material.
The pure and solid metal melting occurs at a certain fixed temperature called the melting point while impure metal materials, it is melting at a different temperature that varies depended on the type and impurity percentage.
As the heart of the foundry, the melting metal process provides molten fluid that can be used to pour into the mold and solidifies into a range of shapes as required. Metal melting is a high energy-consuming work that takes accounts for 55% of the energy consumption of the metalworking industry.
It is a very crucial step because metal melt not only provides the material for the casting process but also affects greatly on physical and chemical of the final casting products.
The melting metal process
Those wonders how to melt metal in foundry can find the melting metal process generally involved these steps as brief:
- Deciding the metal mixed ratio
- Preparing and loading the metal
- Melting the metal
- Refining and treating the molten metal
- Transport the molten metal
Deciding the metal mixed ratio
Each casting application requires different metal mechanical properties that can be changed by adjusting the metal mixture ratio. Casting foundry manufacturer has a formula for metal mixing in accordance with specific material class and requirements.
For example, the material mixing ratio for casting aluminum part in our metal foundry is often 40% Aluminum Ingot + 50% Aluminum scrap + 10% others. In which 10% of others are some additive materials such as alloys of Zn, Mn, Cu, Si, etc.
Preparing the metal
Ingots and scrap metal are main material composition used in the melting process taking up to 80% of the mixing ratio.
Before loading into the furnace, ingots and metal scraps (cans, scrap machinery parts, containers, or sidings) require to be removed dirt plus preheated and dried. This step is to remove the moisture, prevent the exploration possibility in the furnace, limit the slag formation, and enhance the melting capacity.
Particularly with scrap metal, it requires removing the paint, machining oil, and other contaminants, commonly by the thermal process.
Loading and melting the metal
The furnace is charged by adding a fuel source (charcoal, natural gas, electricity). Metal is continuously loading into the furnace in the heating process instead of the batch to save the energy consumption and work effectiveness.
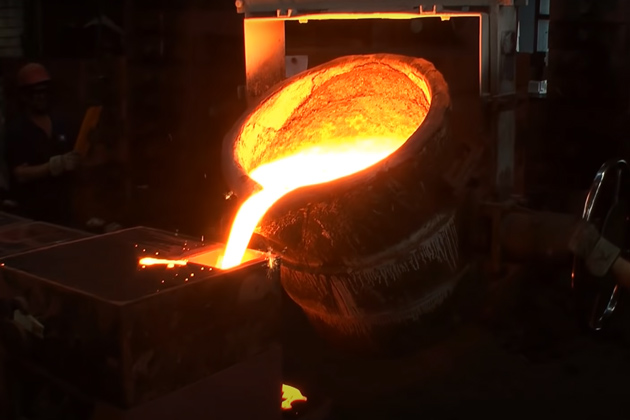
The furnace runs in an extremely hard environment where molten metal, furnace linings, atmospheric gases, and products from combustion of fuels are at very high temperature that requires strictly protection equipment for the worker. Furnace comes in a different size, shape, working principle, and energy so that the melting capacity of each furnace differs from others.
At a fixed melting point, metal transforms from solid to liquid. The melting point varies from metal to metal, ranges from about 350oC to 2000oC.
Refining and treating the molten metal
This process is to degas the melt, take out of undesirable solid sort, and adjust the alloy composition as expected. Additive materials especially some ferrous to increase the mechanical properties of the metal liquid (strength, ductility, rigidity, elasticity).
This step is very crucial because it can affect the final casting quality.
Transport the molten metal
After melting, the molten liquid is transfer from the furnace to the molding line by pouring system.
Melting metal technologies
The heart of the melting metal process relies on the melting furnace directly involving and affecting the melting process effectiveness. There are different melting technologies that affect how to melt metal and decided by which furnace is in use.
How to choose a melting furnace
The melting furnace greatly affects not only the operational effectiveness of the foundry but also the final casting results, hence it is very vital to take into consideration which furnace technologies should apply.
As you know that the metal melting furnaces vary in shape, geometry, fuel and capacity.
These below factors are strictly decide which melting furnace suits on your foundry operation.
- Space availability: Check your production area. Where you will put the furnace?
- Type of alloys to be melt and its melting point
- Melting capacity and metal quantity
- Energy efficiency
- Capital investment
- Operation Cost
- Maintenance requirement
- Emission and environment issue
Of course, there is no one-fit-all option but the casting foundry manufacturers have to consider which criteria are more important than others. Each metal casting foundry will have their own priority criteria to choose the melting furnace that matches their demand and production scale.
After clarifying these considerations, the second step is to select the one working on your casting foundry. Here we sort out the most popular melting furnaces in metal foundries today. Let’s check it.
Current and emerging melting furnace technologies in metal foundry
For melting metal in the metalworking, different types of furnaces are used. They are classified according to the heating source, operating properties, and furnace construction.
The crucible and cupola furnaces are traditional melting methods while induction and electric Arc furnaces are the modern advanced melting technologies.
Crucible Furnace
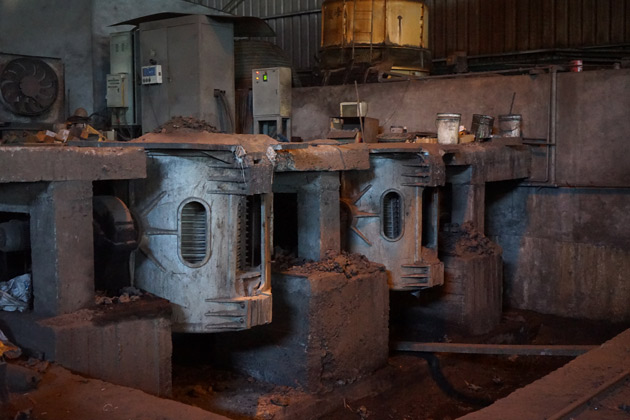
Crucible furnace is the very oldest, simplest, and most original melting vessel that used in the metalworking foundries. This basic melting device is made of high temperature-resistant materials that often are ceramic or refractory substances.
The crucible furnace can come in a very small cup that usually used for melting jewelry (gold, silver) to a bigger container that applies for small batch work.
Crucible heating fuel is usually coke, gas, oil, or electricity. While the electric crucible has a max capacity of 2.5 ton/h, the gas or liquid fuel crucible can melt up to 4 ton/h.
Crucible furnace is not an energy efficiency device with over 60% of heat loss for radiation.
This furnace is suited for non-ferrous metal that especially applied for aluminum melting. They perform well on any aluminum alloys. One advantage is that crucible is very easy to operate and maintain hence save the cost. Plus its low capital cost attracts small casting foundries to invest their money.
However, this furnace only suites on small production volume and low melting point metal due to its low energy efficiency.
Cupola furnaces
Cupola furnace is considered as one of the most economic melting technologies. Almost grey iron nowadays is melted by this furnace.
Construction speaking, the cupola can be made in any shape and size, but its diameter can range from 0.5 to 4m and its height is about 6-11m. The cupola is built as a vertical and cylinder vessel likely a big chimney.
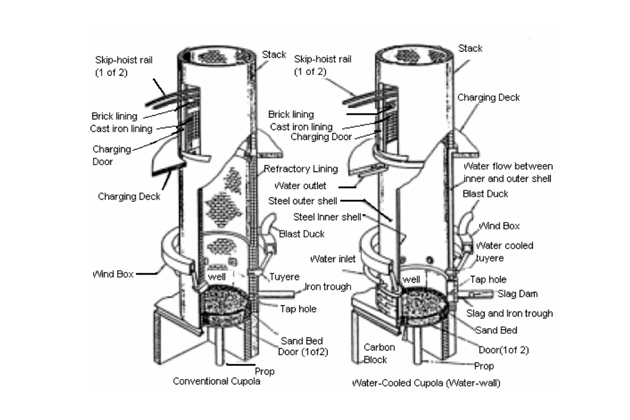
The cupola furnace wall is usually made of steel and is lined with a refractory brick wall. The bottom of the furnace is lined in a similar manner but often uses a mixture of clay and sand since this lining is only temporary. Some cupolas are fitted with cooling shell layers to keep it cool and being added oxygen to make the coke burn more intense.
The heating fuel of the cupola furnace is coke and some additives. To start a production batch, coke layers are added into the furnace and lit with a torch. When the coke ignites, the air is introduced into the coke layers through the vents. Wood, coal, or combustible gases can also be used as furnace fuel.
When coke is enough hot, solid metals are fed into the furnace through the hole in the top. During the melting process, the thermodynamic reaction takes place between the fuel and the inlet air.
The carbon in the coke combines with the oxygen in the air to create carbon monoxide, which continues to burn to carbon dioxide. A certain amount of carbon dissolves into the falling liquid metal droplets and hence, increases the carbon content in the metal. This melting process produces different types of the grade of iron and steel.
Cupola furnace can apply to melt any ferrous, mostly used for iron melting with big volume. Statistically, 60% of iron casting is melt by a cupola. Its energy efficiency is also high, take account of about 40-70%.
Electric Arc Furnaces
Electric arc furnace (EAF) is a furnace that uses energy of an electric arc to heat and melt the material.
It ranges from 1 ton (usually to produce pig iron) to 400 tons (for secondary steel). Industrial electric arc furnaces can reach temperatures of 1,800° C (3,272°F) while laboratory vessels can reach over 3,000° C (5,432°F).
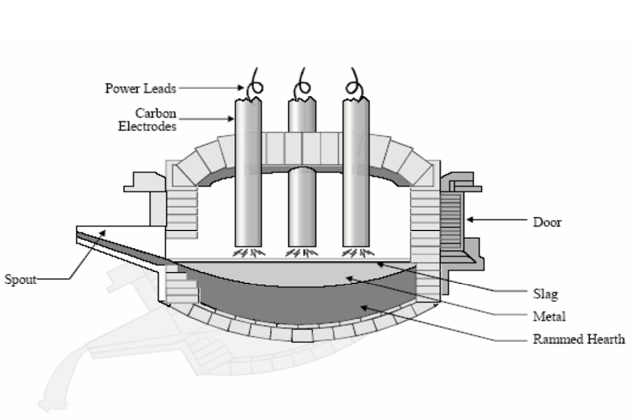
How to melt metal by the electric arc furnace?
In the electric arc furnace, the material is in direct contact with the arc electricity and the electric current passes through the material. Hence, the melting is more effective than other technologies that use external heat.
The electric arc furnace is often used to melt steel (take account of 87%) while 13% is to melt iron. They can process steel automobile shredded scrap included high residual elements well that will not be effective by cupola melting.
Induction furnace
An induction furnace is an electric furnace using the principle of electromagnetic induction. So how to melt metal by this melting technology?
Metal is loaded into the crucible that surrounds by the copper coil of wire carrying alternating electric current. Once the induction furnace turned on, the coil creates a reversing magnetic field rapidly that penetrates over the metal. The magnetic field creates eddy currents, a circular electric current running inside the metal. As result, these currents’ circulation creates very high temperatures that melt the metals.
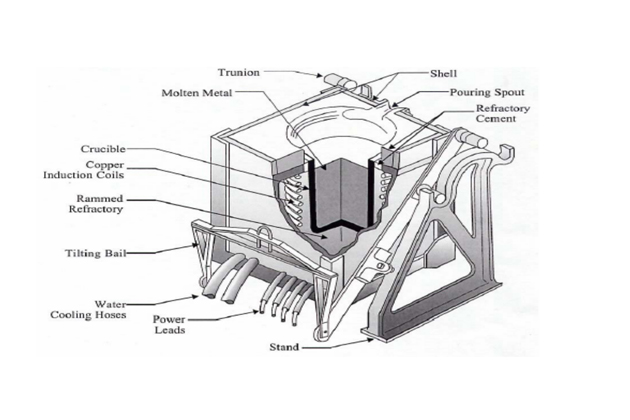
The melting capacity of induction furnaces ranges from less than 1 kg to 100 tons, commonly used to melt iron, steel, copper, aluminum, and precious metals.
Compared with other metal smelting technologies, the advantage of induction furnaces is that it is clean, energy-efficient, and easy to control the melting process.
However, induction furnace limits in metal scrap types and some alloy elements might be loss because of oxidation.
Metal melting points
Most of the metals that exist on earth have their normal state as solid. However, in metalworking industries, especially metal casting and metallurgy, the metal needs to be liquefied to produce a new product. In order to liquefy metal, it is necessary to heat the metal to its melting point.
Therefore, it is as same important as how to melt metal to know the melting temperature of substances. It makes metal casting processing simpler. Experts can accurately calculate the molding, fusing, and freezing time of casting products. This helps inefficient production, at the same time, bring the necessary backup solutions for your work to handle emergencies.
What is the melting point?
The melting point, also known as the liquefaction temperature, is the temperature at which the melting process of a solid metal takes place. It is the point at which metal transform from the solid phase to the liquid phase. The melting point varies from metal to metal.
In practice, the melting point is considered relative. It is insensitive to pressure. Some amorphous substances such as glass do not have a fixed melting point.
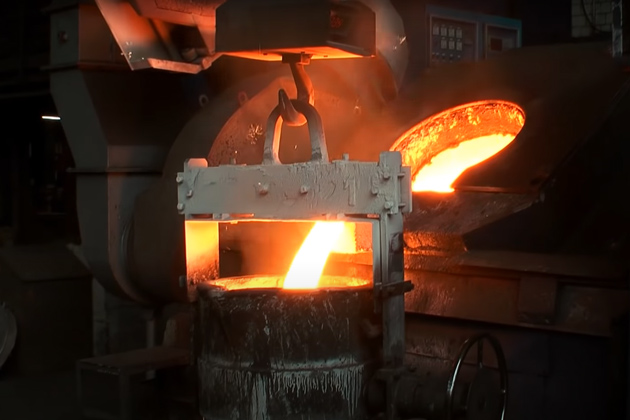
Which metal has the highest melting point?
Volfram (W), as known as Tungsten, is the metal with the highest melting point (3,422°C; 6,192°F), the lowest vapor pressure (at temperatures above 1,650°C, 3,000°F) and the highest tensile strength.
Easiest metal to melt
Up to this point, the metal with the lowest melting point is mercury with a melting point of – 38.830C. It is the only metal on earth in a liquid state under normal, standard chemical temperature and pressure conditions.
Currently, mercury’s main application is for use as thermometer, pressure, manometer, float valve, mercury switch, etc.
Melting point of iron and steel
Iron is the most used metal in the world today, taking account for 95% of the total annual metal production.
Pure iron is soft and flexible. But when adding the carbon component at the rate of 0.002% – 2.1%, it will create a steel alloy with outstanding hardness, ductility, and bearing capacity.
Iron has a melting point of 1538°C while that of steel is 1370°C. Currently, iron and steel are two metals that are used a lot in the field of mechanical manufacturing, automobile industry, shipbuilding, construction, etc.
Aluminum melting point
Aluminum has a melting point of 933.47K (660.32 ° C; 1220.58 ° F). Aluminum’s melting point is not high compared to other metals.
In the periodic table, aluminum is denoted Al; Atomic number is 13, density 2.9 g / cm3. Aluminum is light in weight, soft, and excellent corrosion resistance and good cast-ability. It is the most common metal in the Earth’s crust. Aluminum casting is widely used in machine details, engines, and exterior urban decoration.
Metal | melting point (° C) | melting point (°F) |
Aluminum | 660.32 | 1220.58 |
Aluminum Alloy | 463 – 671 | 865 – 1240 |
Iron, Wrought | 1482 – 1593 | 2700 – 2900 |
Iron, Gray Cast | 1127 – 1204 | 2060 – 2200 |
Iron, Ductile | 1149 | 2100 |
Lead | 327.5 | 621 |
Magnesium | 650 | 1200 |
Carbon Steel | 1425 – 1540 | 2600 – 2800 |
Stainless Steel | 1510 | 2750 |
Protective safety guidance in the melting metal process
Melting metal process daily has to deal with extreme heating (could up to 2000° C) that is very hazard working environment.
It can say that melting is one of the most dangerous works that cause unexpected accidents in metal foundries. Read more about How metal foundry work.
Hence, to protect health and life for the worker and avoid loss and damage to the foundry’s properties, there is strict guidance that metal casting foundries manufacturers have to take into consideration.
Ensure foundry infrastructure
- The melting area must be arranged separately to avoid danger to non-authorized workers
- There must be ventilation and the foundry roof design must be high for air circulation
- The furnace must ensure quality and safety when used
- Should be equipped with an automatic or semi-automatic system to pour and refuel to limit human exposure and accidents.
- Explosion and fire-proof equipment must be always ready
Ensure the protective safety clothes for the worker
The melting worker must be equipped with full protection clothes while in shift. Hat, glasses, glove, mask, thick clothes and shoe are compulsory accessories.
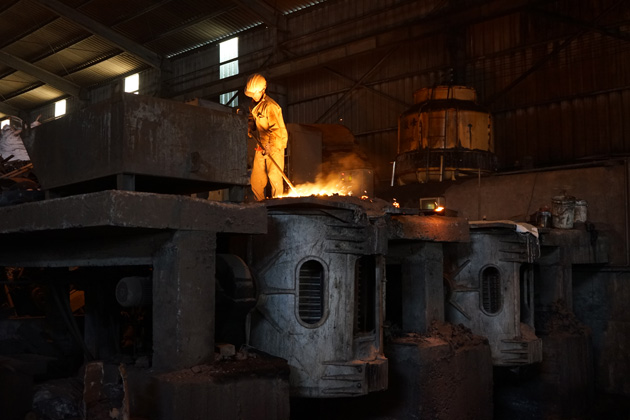
Dos and don’ts
- Do put caution sign for the melting zone
- Do restrict unauthorized workers access the melting zone
- Do regularly check the furnace and ventilation system and ensure ineffective one repaired immediately
- Do clean and dry metal material before melting
- Do preheat furnaces and refractories before use
- Do prepare Emergency Plan
- Don’t allow smoking, eating, drinking in the melting zone
Summary
Through the above content, we have provided a detailed explanation of How to melt metal in a foundry. Hopefully, it will update you on some interesting ideas on the melting metal process.
Read more about our blog over the casting procedure in the metalworking foundries here.
Short introduced, VIC is the metal casting foundry manufacturer that specializes in manufacturing and supplying metal casting parts to the world market. If you are in need, do contact us to place an order and get advice on casting treatment.
Reference
US Department of Energy (2005). Advanced Melting Technologies: Energy Saving Concepts and Opportunities for the Metal Casting Industry.https://www.energy.gov/sites/prod/files/2013/11/f4/advancedmeltingtechnologies.pdf.
Safe Work Australia (2013). Guide to Managing Risks Associated with Foundry Work. https://www.safeworkaustralia.gov.au/system/files/documents/1702/guide-managing-risks-associated-foundry-workl.pdf
Excellent article with simplified manner to cover all topics related to a Foundry. Great job
Good